Settingsun
Structural
- Aug 25, 2013
- 1,513
I was at a construction site on other business and noticed ‘stacked’ beams used for temporary works. Working from floor level upwards, there were: a pair of I-beams at 5~6m centres (depth:width is about 2.5 for this size of beam); then a square hollow section on top of the I-beams (ie spanning between the I-beams, loading them at midspan); then a temporary post at midspan of the hollow section. If you looked in plan, the system would be the shape of the letter H. No bolts or welds that I could see, everything was just sitting on everything else.
Putting aside rigid-body stability, I’m interested in the lateral-torsional buckling capacity of the I-beams. I found an old topic on this forum with a pointer to British Standard BS5950 which gives about a 20% increase in effective length compared with a beam where the bottom flange is bolted down. See the bottom two rows in the table.
I also have a guideline from the Australian Steel Institute’s journal which gives no penalty compared with having the bottom flange bolted down. See the image below. For comparison to BS5950, partial restraint with top flange loading (destabilising) in Australia gives an effective length of around 1.1*1.4*L, which is pretty close to the 1.4L + 2D from the British code, while ‘normal’ load would give 1.1*1.0*L. The 1.1 factor varies slightly depending on geometry in both cases but is usually 1.0-1.2.
I’m interested in other references, rules of thumb, gut feels etc. Zero to 20% penalty seems a little low to me.
Putting aside rigid-body stability, I’m interested in the lateral-torsional buckling capacity of the I-beams. I found an old topic on this forum with a pointer to British Standard BS5950 which gives about a 20% increase in effective length compared with a beam where the bottom flange is bolted down. See the bottom two rows in the table.
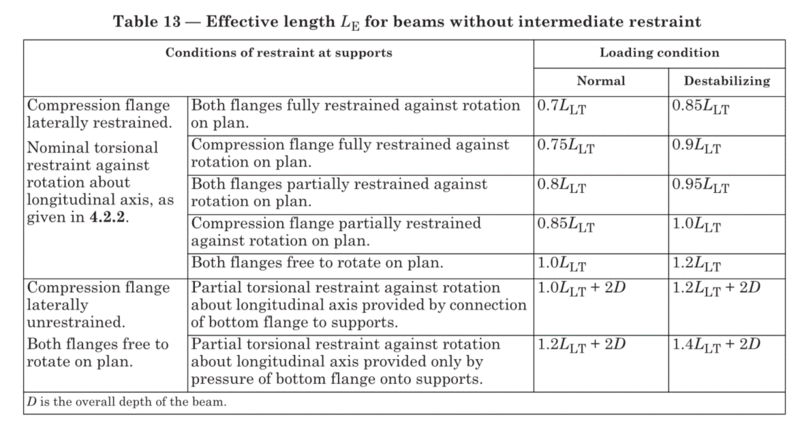
I also have a guideline from the Australian Steel Institute’s journal which gives no penalty compared with having the bottom flange bolted down. See the image below. For comparison to BS5950, partial restraint with top flange loading (destabilising) in Australia gives an effective length of around 1.1*1.4*L, which is pretty close to the 1.4L + 2D from the British code, while ‘normal’ load would give 1.1*1.0*L. The 1.1 factor varies slightly depending on geometry in both cases but is usually 1.0-1.2.
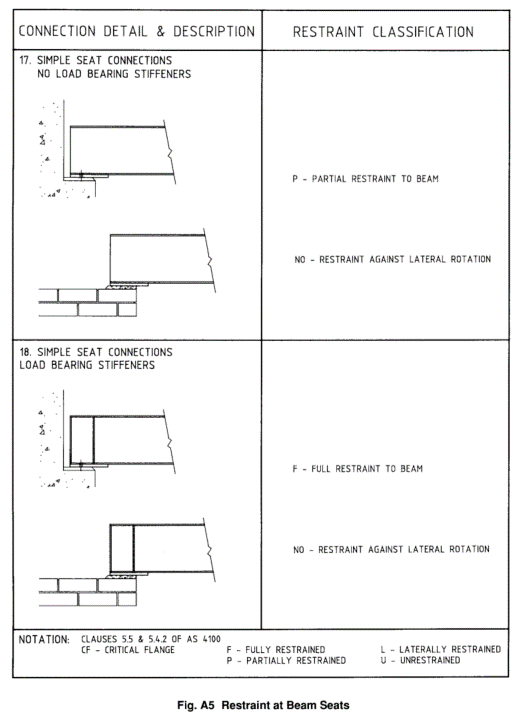
I’m interested in other references, rules of thumb, gut feels etc. Zero to 20% penalty seems a little low to me.