ZachTheEngineer
Mechanical
Hello everyone this is my first post!
High-level question about magnet arrangements and which might create a stronger adhesion force. I am using an alternating polarity arrangement because I have tested that to be the strongest. The air gap (ground clearance) between the magnet faces and the thick steel wall is 0.4 inches. Also, there is a 0.1-inch thick steel shielding plate that also acts as a yoke. Mathematically, will arrangement 1 or 2 generate the strongest adhesion force at this ground clearance? Thanks for any input!
High-level question about magnet arrangements and which might create a stronger adhesion force. I am using an alternating polarity arrangement because I have tested that to be the strongest. The air gap (ground clearance) between the magnet faces and the thick steel wall is 0.4 inches. Also, there is a 0.1-inch thick steel shielding plate that also acts as a yoke. Mathematically, will arrangement 1 or 2 generate the strongest adhesion force at this ground clearance? Thanks for any input!
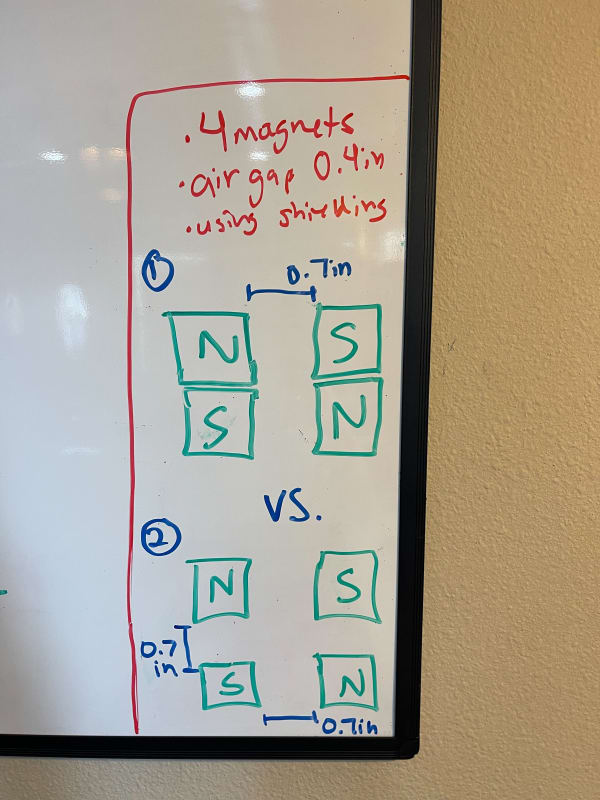
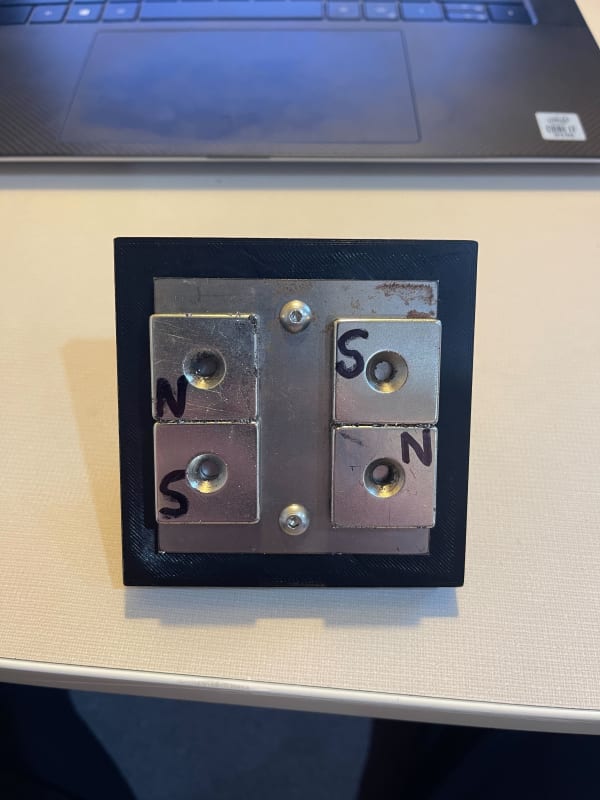
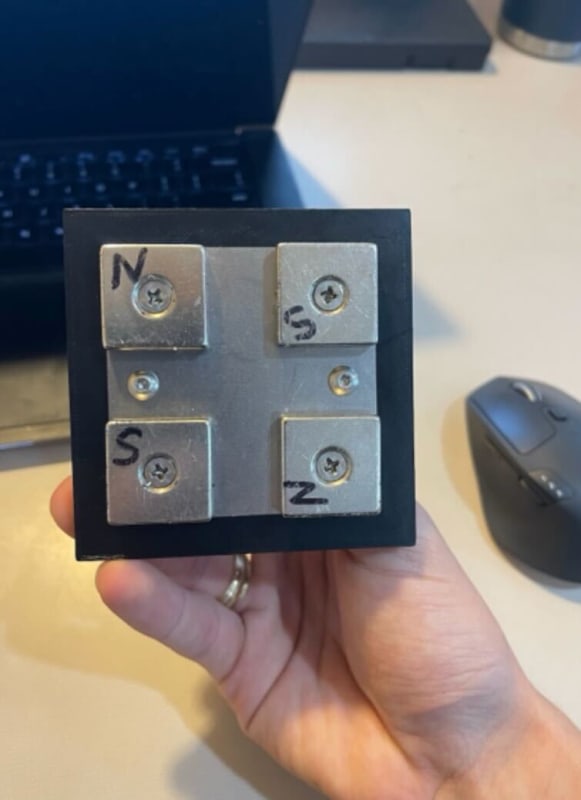
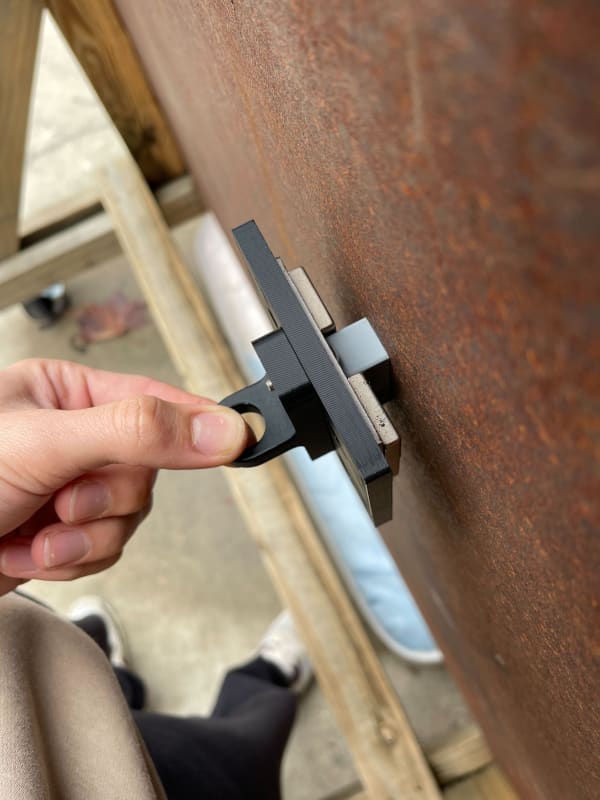