All,
You may recall the challenges I was facing with installing a fuel injector in every cylinder of my engine; with a 49.5cc engine comprised of 6 cylinders, each was only 8.25cc and required a micro-fuel injector that had good enough spray pattern to yield a well mixed homogeneous fuel/air mixture. After working through the injector design, I decided the injector approach was simply too risky for a small engine such as my prototype. I thus went off to work up an alternate architecture using a single larger fuel injector to feed an intake manifold shared between all cylinders. This puts the fuel injector into the realm of components I can buy off-the-shelf.
The use of a shared intake manifold with premixed fuel/air unfortunately requires use of two air pump pistons in place of the one in the prior architecture; one air pump piston for scavenge fed with air alone and another for intake fed with mixed fuel and air. The use of separate pistons increases complexity because each must now be driven by independent cam lobes (not a big deal) but the two pistons don't affect performance much because the pistons are very light and operate at comparatively low pressure. They do, of course add some volume, but not as much as I expected. Since I was reworking everything, I decided to exploit the separate cams on intake and scavenge to mechanize over expansion (to increase efficiency) and simplify the means by which I was compensating for cold-start and altitude (which both require variable compression ratio). All of these changes are evident in the annotated illustration below.
While I'm bummed at the amount of work this change is taking to update math models, CAD models, CFD, and FAE, I'm happy with the performance and glad to have caught the problems in the prior architecture *before* I started cutting metal!
Comments, suggestions, and questions are encouraged!
Rod
You may recall the challenges I was facing with installing a fuel injector in every cylinder of my engine; with a 49.5cc engine comprised of 6 cylinders, each was only 8.25cc and required a micro-fuel injector that had good enough spray pattern to yield a well mixed homogeneous fuel/air mixture. After working through the injector design, I decided the injector approach was simply too risky for a small engine such as my prototype. I thus went off to work up an alternate architecture using a single larger fuel injector to feed an intake manifold shared between all cylinders. This puts the fuel injector into the realm of components I can buy off-the-shelf.
The use of a shared intake manifold with premixed fuel/air unfortunately requires use of two air pump pistons in place of the one in the prior architecture; one air pump piston for scavenge fed with air alone and another for intake fed with mixed fuel and air. The use of separate pistons increases complexity because each must now be driven by independent cam lobes (not a big deal) but the two pistons don't affect performance much because the pistons are very light and operate at comparatively low pressure. They do, of course add some volume, but not as much as I expected. Since I was reworking everything, I decided to exploit the separate cams on intake and scavenge to mechanize over expansion (to increase efficiency) and simplify the means by which I was compensating for cold-start and altitude (which both require variable compression ratio). All of these changes are evident in the annotated illustration below.
While I'm bummed at the amount of work this change is taking to update math models, CAD models, CFD, and FAE, I'm happy with the performance and glad to have caught the problems in the prior architecture *before* I started cutting metal!
Comments, suggestions, and questions are encouraged!
Rod
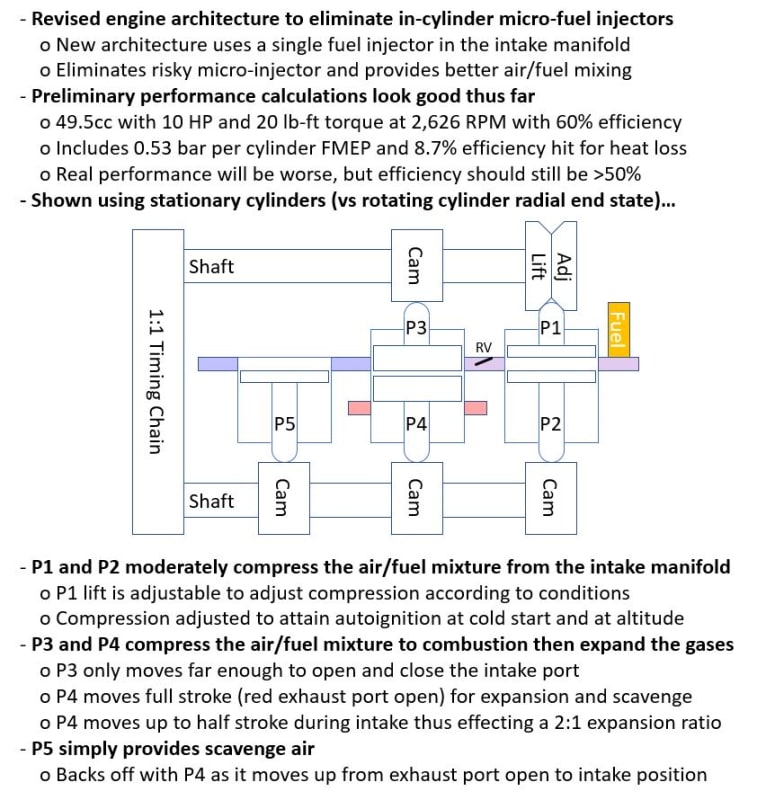