gersen
Materials
- Nov 14, 2017
- 27
Hello
at work we had a problem with some pieces.
We made 4 pieces like the picture below using a oxycutted plate th. 650 mm material 1.0577.
We machined a hole Ø500 +0.1, but after few weeks the hole has an eccentricity of 1 mm.
Can the cause of this be residual stresses inside the material? Should we have made a stress relieving tratment beforehand?
I gladly read your opinions on this.
at work we had a problem with some pieces.
We made 4 pieces like the picture below using a oxycutted plate th. 650 mm material 1.0577.
We machined a hole Ø500 +0.1, but after few weeks the hole has an eccentricity of 1 mm.
Can the cause of this be residual stresses inside the material? Should we have made a stress relieving tratment beforehand?
I gladly read your opinions on this.
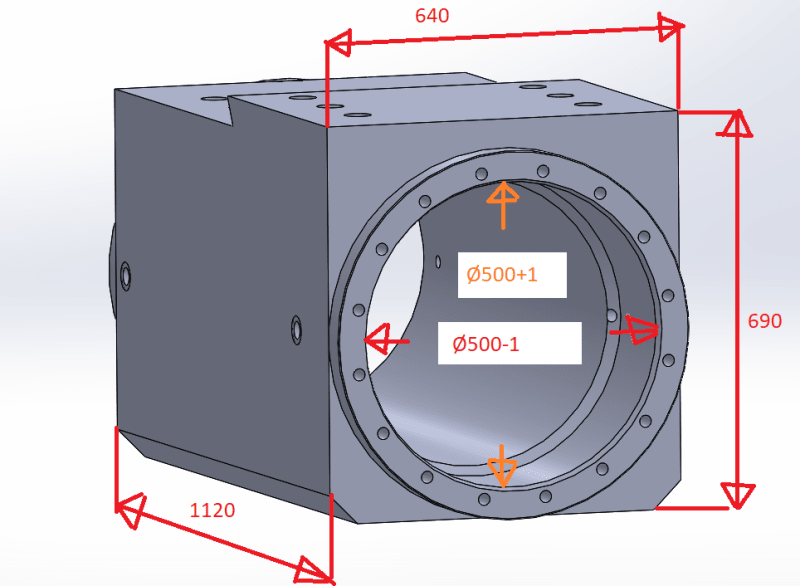