Vikram 1971
Industrial
Below is the image of a hot steel rolling mill roll having V Groves.
I am trying to measure the length of each side of the grove as shown in the figure accurately.
Currently I am using a normal ruler but as you can see it not accurate.
Any other proper way of measure the grove length accurately, hence checking the symmetry of the groves????
(Any different tool or caliper? ?)
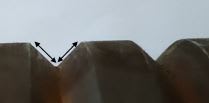
I am trying to measure the length of each side of the grove as shown in the figure accurately.
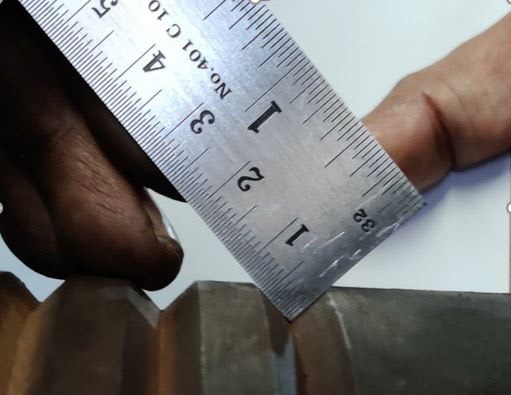
Currently I am using a normal ruler but as you can see it not accurate.
Any other proper way of measure the grove length accurately, hence checking the symmetry of the groves????
(Any different tool or caliper? ?)