Hello All,
We have a multi stage split case boiler feed pump that is failing again and again on mechanical seals. Evidently, there is solid build up of process fluid in the seal camber and around seals. Here are few pictures. Here are pump rated conditions: 550 GPM, 3560 RPM, 3115 Feet Rated head. Can you comment on the root cause and what can be the solution?
We have a multi stage split case boiler feed pump that is failing again and again on mechanical seals. Evidently, there is solid build up of process fluid in the seal camber and around seals. Here are few pictures. Here are pump rated conditions: 550 GPM, 3560 RPM, 3115 Feet Rated head. Can you comment on the root cause and what can be the solution?
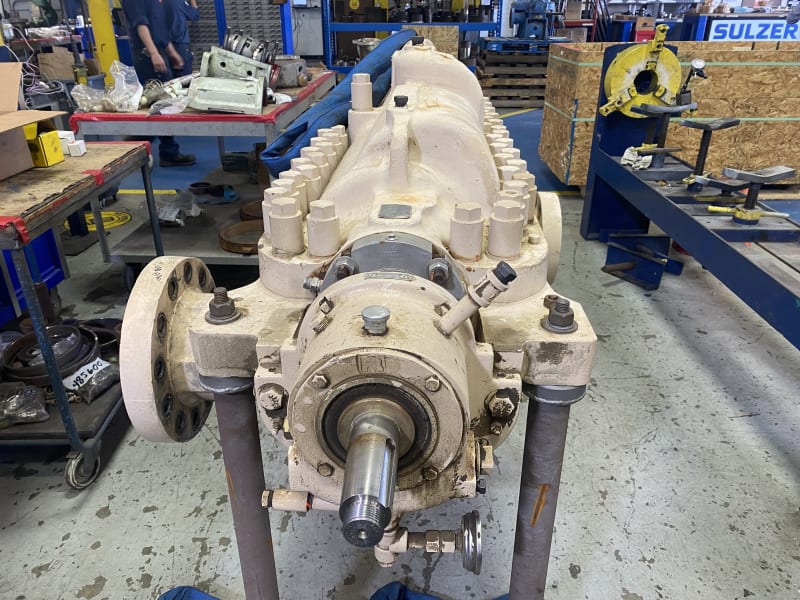
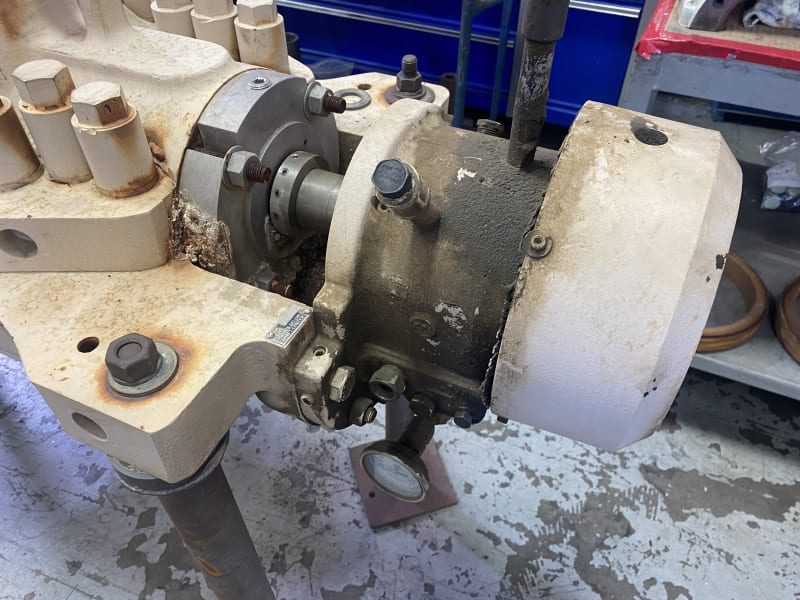
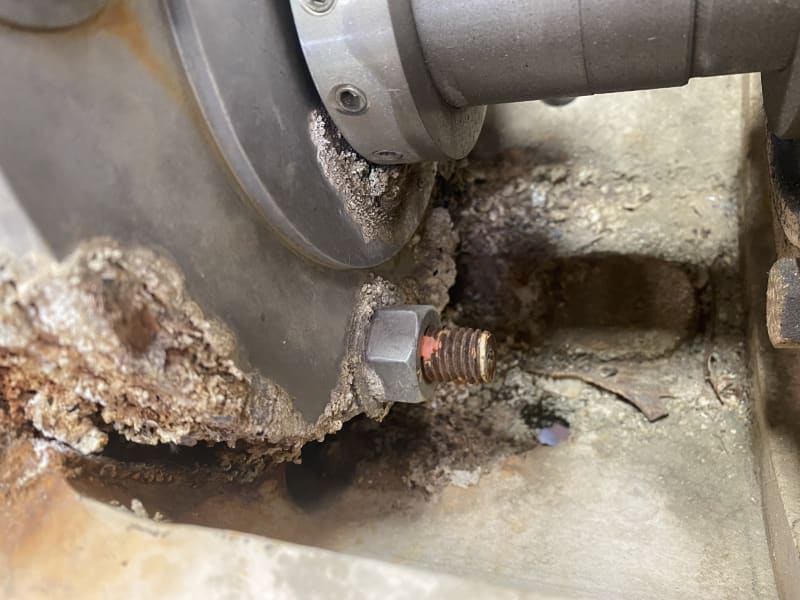
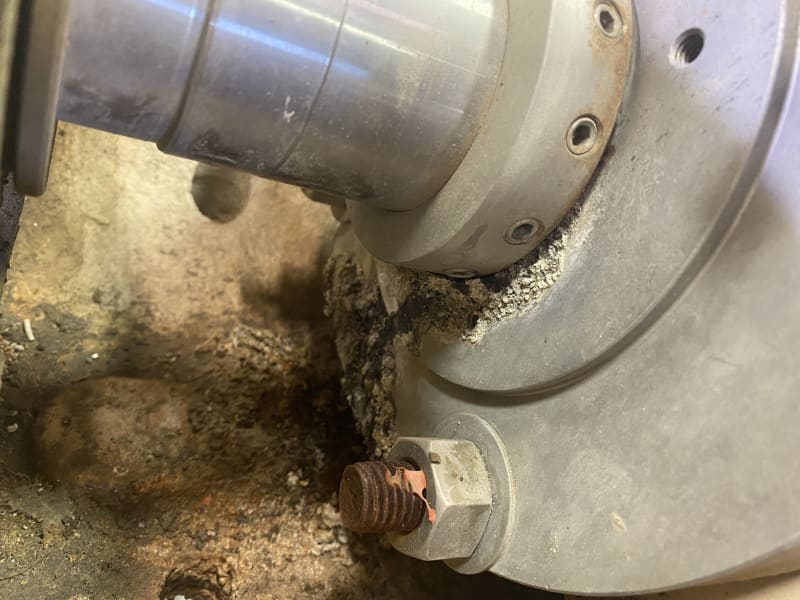