humaidq
Mechanical
- Mar 31, 2006
- 2
Hi All,
I am fairly new in terms of dealing with Mechanical Seal and would like to know how I can calculate the flow rate if the seal fails. I have attached a picture of a mechanical seal that I am working with.
I am fairly new in terms of dealing with Mechanical Seal and would like to know how I can calculate the flow rate if the seal fails. I have attached a picture of a mechanical seal that I am working with.
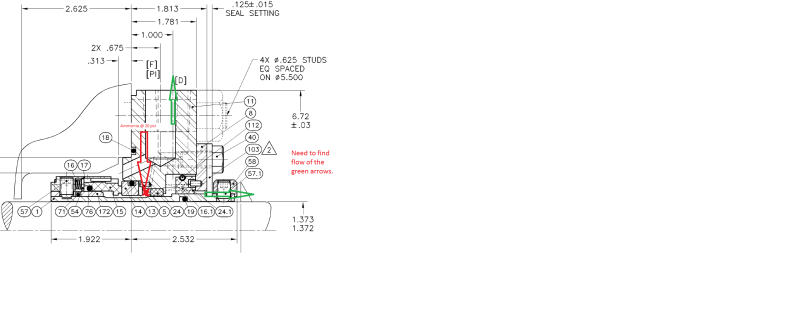