Dear Colleagues,
Looking for some advice. On the plant where I work, we have an API 610 VS4 pump. The pump is having high vibration only in one radial direction (almost 6mm/s - too high for a newly commissionned mechine), while axial and other radial vibration are within ISO limits.
This pump was originally supplied with lubrication to the bushings from the same discharge of the pump. Our first thought was that during commissioning stage the process fluid was not clean enough and could bring some particles to the carbon bushings. so we dissasembled the pump, we found some corrosion and therefore we fabricated new bushings. Also we changed the lubrication method to have external treated water line. Despite these efforts, the pump is still having high vibration as shown in the attached spectra.
I would like to ask your advice and recommendations on:
1. If with available vibration measurement is possible to have any conclusion on the possible causes.
2. What additional vibration measurement (phase, nyquist, etc) could give more light on the root cause.
Appreciate any help
Looking for some advice. On the plant where I work, we have an API 610 VS4 pump. The pump is having high vibration only in one radial direction (almost 6mm/s - too high for a newly commissionned mechine), while axial and other radial vibration are within ISO limits.
This pump was originally supplied with lubrication to the bushings from the same discharge of the pump. Our first thought was that during commissioning stage the process fluid was not clean enough and could bring some particles to the carbon bushings. so we dissasembled the pump, we found some corrosion and therefore we fabricated new bushings. Also we changed the lubrication method to have external treated water line. Despite these efforts, the pump is still having high vibration as shown in the attached spectra.
I would like to ask your advice and recommendations on:
1. If with available vibration measurement is possible to have any conclusion on the possible causes.
2. What additional vibration measurement (phase, nyquist, etc) could give more light on the root cause.
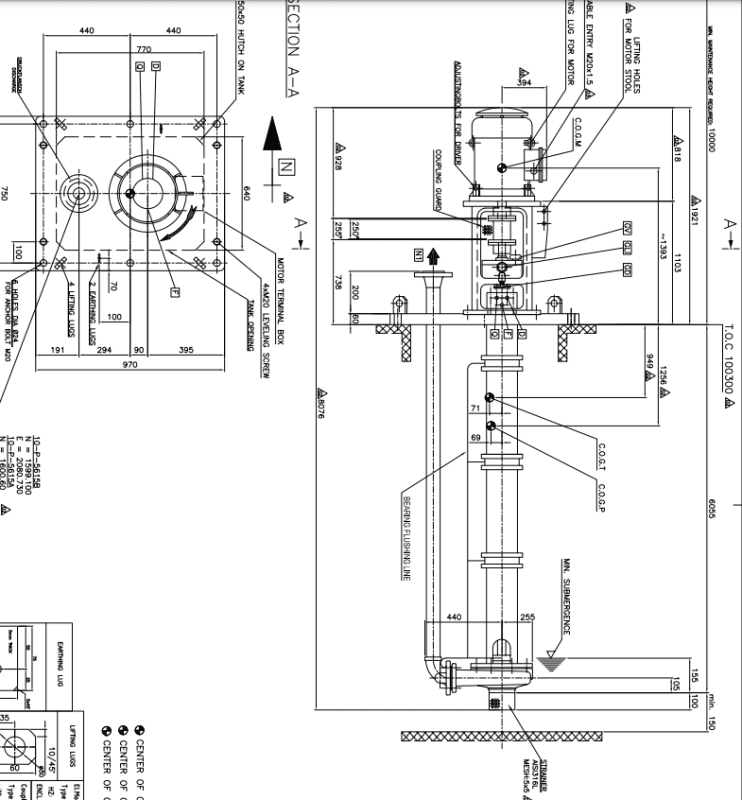
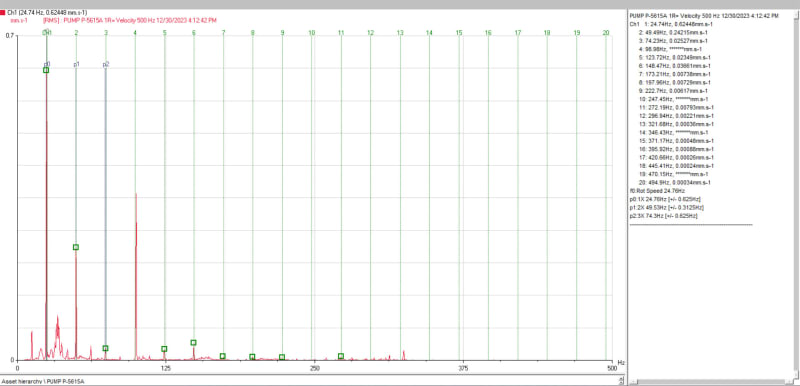
Appreciate any help