Hi, I have a simple upstream wellsite facility design, shown in the below image.
Liquid comes from an HP separator (not shown) into the heater operating at 50 psig, 120F. The pressure on the heater is maintained by the back pressure valve set at 50 psig. The separated oil from the heater goes to the atmospheric oil tank. The water line is irrelevant here.
There are two gas lines: one from the atmospheric oil tanks (0 psig) and other from the heater (50 psig). My colleague came up with a design of merging these two lines into one, therefore capturing flash vapors from tanks and the heater through a single VRU (oil flooded screw compressor). The suction control valve will maintain the inlet pressure to the VRU in the range of 0.4~0.8 oz. I'm curious how the two gases from different pressure vessels will merge together. There will be check valves from both sides to prevent back-surge.
Q1) Will the vapors from tank be able to smoothly merge with 50 psig heater gas, and flow into the VRU suction together?
Q2) Will the 50 psig pressure from the heater exert back pressure on the tanks, causing it to vent to air instead of flowing into the VRU suction?
Q3) If this is not gonna work well, what can be down to remedy this?
Q4) bonus question, but if anyone has an example vapor recovery P&ID and can share with me, that would be great (aegis4048@gmail.com)
I'm asking this because usually there's a separate booster compressor for heaters (30~50 psig) and another VRU for tank & VRT vapors (0~3 psig).
Liquid comes from an HP separator (not shown) into the heater operating at 50 psig, 120F. The pressure on the heater is maintained by the back pressure valve set at 50 psig. The separated oil from the heater goes to the atmospheric oil tank. The water line is irrelevant here.
There are two gas lines: one from the atmospheric oil tanks (0 psig) and other from the heater (50 psig). My colleague came up with a design of merging these two lines into one, therefore capturing flash vapors from tanks and the heater through a single VRU (oil flooded screw compressor). The suction control valve will maintain the inlet pressure to the VRU in the range of 0.4~0.8 oz. I'm curious how the two gases from different pressure vessels will merge together. There will be check valves from both sides to prevent back-surge.
Q1) Will the vapors from tank be able to smoothly merge with 50 psig heater gas, and flow into the VRU suction together?
Q2) Will the 50 psig pressure from the heater exert back pressure on the tanks, causing it to vent to air instead of flowing into the VRU suction?
Q3) If this is not gonna work well, what can be down to remedy this?
Q4) bonus question, but if anyone has an example vapor recovery P&ID and can share with me, that would be great (aegis4048@gmail.com)
I'm asking this because usually there's a separate booster compressor for heaters (30~50 psig) and another VRU for tank & VRT vapors (0~3 psig).
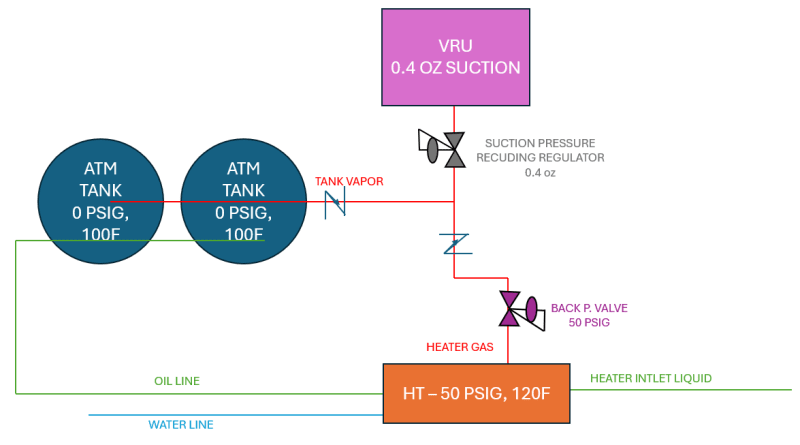