I wonder which is the most theoretically better and accurate mesh of a circular section subjected to perpendicular distributed load and with interest in stresses in the whole plane.
I have seen several examples, using either triangular elements only or a mix between triangular and rectangular:
Why is best? Are there better alternatives?
I have seen several examples, using either triangular elements only or a mix between triangular and rectangular:
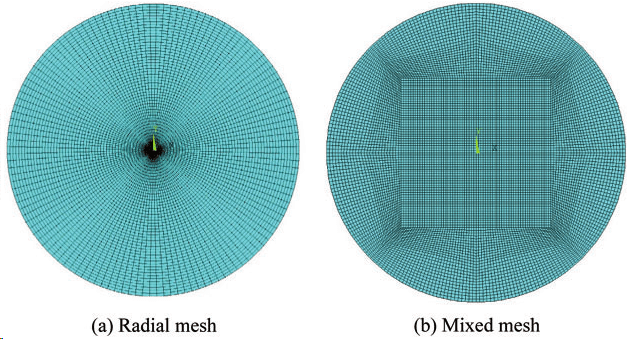
Why is best? Are there better alternatives?