Greetings to all.
I am currently designing a steel framed building with metal roof deck supported by open web steel joist. The roof has a gable profile. The steel joist is spaced at 10 ft and sitting on wide flange girders. Based on my quick calculation, the rollover strength is not enough to transfer the shear to the chord (wide flange girder) thus some forms of shear connector need to be employed.
I came up with the attached detail. Basically, having a HSS shop weld to the top flange of the girder at certain spacing that matches the frequency of the sidelap fastener. And then having a wide bent plate welded to each side of the HSS. So the bent plates can catch the flute without worrying about the field alignment.
I have the following questions and thank you all taking time reading my post.
1. Will this detail work? If not, what will be your suggestions?
2. If goes by this detail, do you think the shear flow at the ridge in the diaphragm is disrupted or can I treat the windward and leeward diaphragm as a whole? I am leaning toward to treating them as a continuous diaphragm because the specified sidelap fastener is satisfied at the ridge.
I am currently designing a steel framed building with metal roof deck supported by open web steel joist. The roof has a gable profile. The steel joist is spaced at 10 ft and sitting on wide flange girders. Based on my quick calculation, the rollover strength is not enough to transfer the shear to the chord (wide flange girder) thus some forms of shear connector need to be employed.
I came up with the attached detail. Basically, having a HSS shop weld to the top flange of the girder at certain spacing that matches the frequency of the sidelap fastener. And then having a wide bent plate welded to each side of the HSS. So the bent plates can catch the flute without worrying about the field alignment.
I have the following questions and thank you all taking time reading my post.
1. Will this detail work? If not, what will be your suggestions?
2. If goes by this detail, do you think the shear flow at the ridge in the diaphragm is disrupted or can I treat the windward and leeward diaphragm as a whole? I am leaning toward to treating them as a continuous diaphragm because the specified sidelap fastener is satisfied at the ridge.
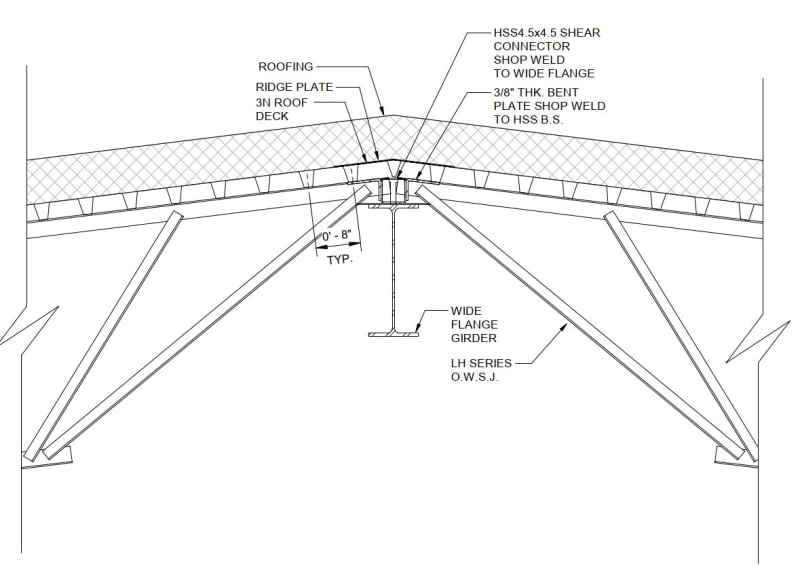