ChiEngr
Structural
- Oct 19, 2021
- 77
Hello,
I have a really difficult connection to detail here, and I am about out of ideas. I am trying to resupport existing steel roof deck (H.H. Robertson Type DC) on a brand new collector beam at the interface of an existing building and new building expansion. I want the connection to be able to transfer in-plane shear loads, but not take any transverse shear loads that could potentially cross the interface via the new roof diaphragm at the new building. Does anybody have any ideas as to how this can be achieved? I was thinking about using 1/4" A307 bolts in slotted holes in the angle, but I have never seen bolts be used to connect light gauge deck to structural steel.
I have a really difficult connection to detail here, and I am about out of ideas. I am trying to resupport existing steel roof deck (H.H. Robertson Type DC) on a brand new collector beam at the interface of an existing building and new building expansion. I want the connection to be able to transfer in-plane shear loads, but not take any transverse shear loads that could potentially cross the interface via the new roof diaphragm at the new building. Does anybody have any ideas as to how this can be achieved? I was thinking about using 1/4" A307 bolts in slotted holes in the angle, but I have never seen bolts be used to connect light gauge deck to structural steel.
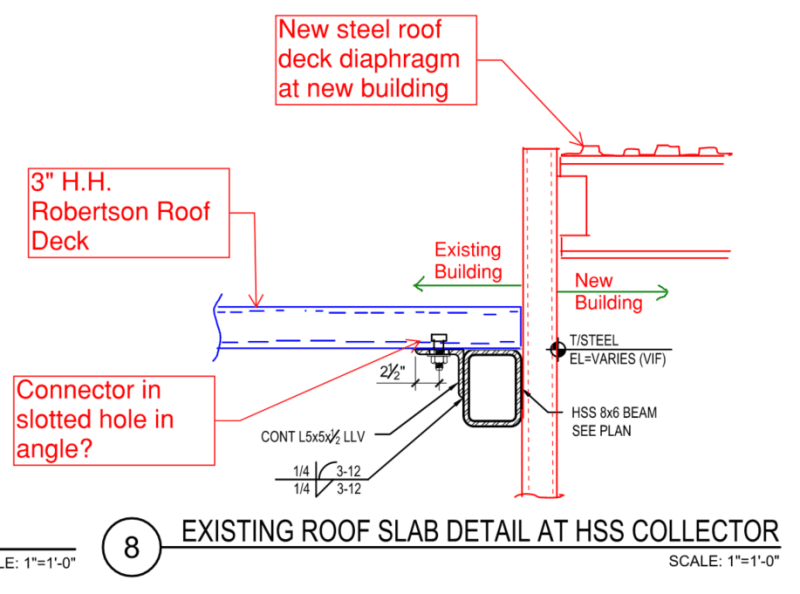