I am trying evaluate methods to permanently retain a small disk, .75" x .125" in some plastic.
I have come up with 3 ideas, but not so sure of the cost effects and manufacturability of each.
Insert disk and sonic weld cap on...Needs to be strong bond.
Drop Disk into slot and Glue/Sonic weld cap to retain
Snap Latch..No so sure about designing these still.
I'd like to permanently retain the disk. I think Molding it in would also be nice, but the disk has a 170degF limit. Don't know the cost of that either..I can possibly substitute for high temperature material.
So I have 4 Options..Need good retention strength. Water tight would be a plus, but Do I have to be concerned if this is brought on an air plane and increased pressure differential causes a break at the seal? Something I have to analyze. Also, I need to be able to predict the sonic weld strength. Mostly thinking out loud here.
Thanks
I have come up with 3 ideas, but not so sure of the cost effects and manufacturability of each.
Insert disk and sonic weld cap on...Needs to be strong bond.
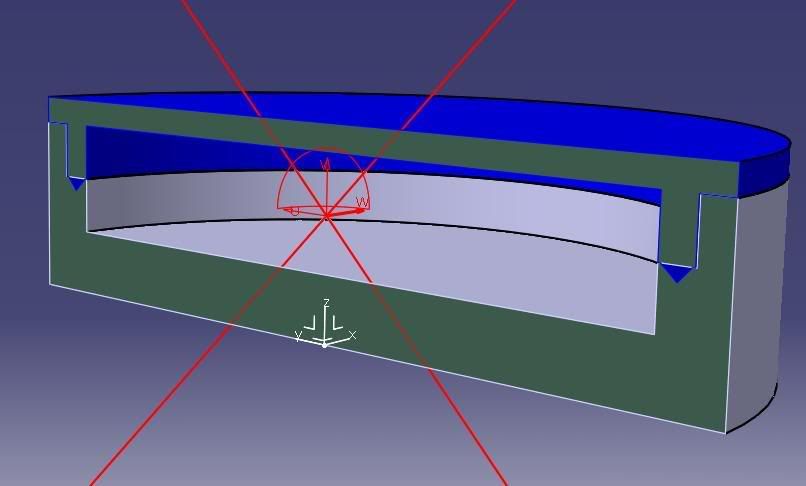
Drop Disk into slot and Glue/Sonic weld cap to retain
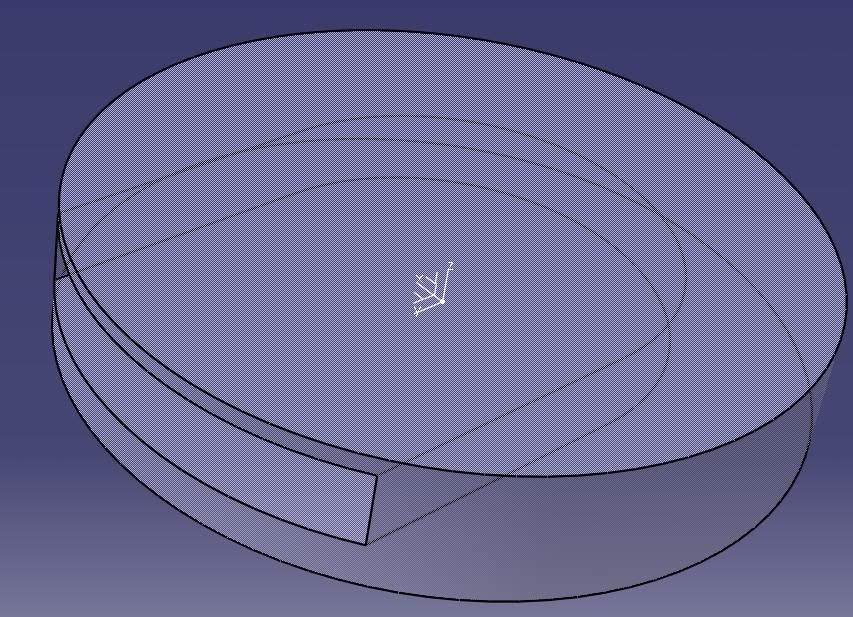
Snap Latch..No so sure about designing these still.
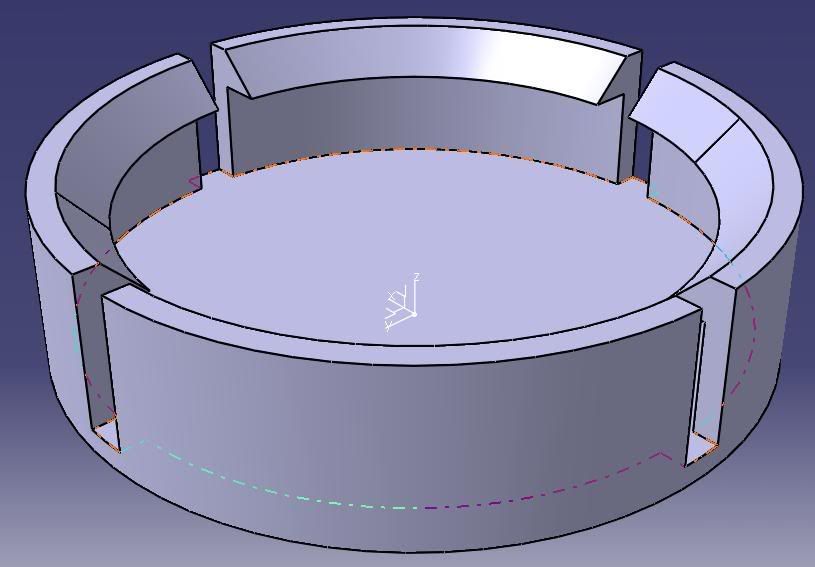
I'd like to permanently retain the disk. I think Molding it in would also be nice, but the disk has a 170degF limit. Don't know the cost of that either..I can possibly substitute for high temperature material.
So I have 4 Options..Need good retention strength. Water tight would be a plus, but Do I have to be concerned if this is brought on an air plane and increased pressure differential causes a break at the seal? Something I have to analyze. Also, I need to be able to predict the sonic weld strength. Mostly thinking out loud here.
Thanks