Jo-
Mechanical
- Oct 10, 2022
- 2
Hello All,
I'm working on a chiller plant replacement project involving the installation of two (2) 180-ton each MultiStack MagLev water cooled chillers (one on standby) that has a designed flowrate of 373gpm thru each chiller. MultiStack has included in their submittal the following requirements (see below) concerning the minimum chilled water flowrates(187gpm) thru the chiller as well as the required minimum (340 Gallons) chilled water bypass loop volume. Have you seen this before, what's the reason for the 2-minute minimum volume in the bypass loop? The building's existing chilled water bypass pipe is located within the chiller mechanical room, we would have to add a chilled water bypass pipe much further downstream of the chilled water pumps to achieve the 340 gallons requirements if there is good reason to it. What's your thought on this?
Also, does the minimum required chilled water flowrate of 187gpm thru the chiller sound correct to you for chiller with design flowrate of 373gpm?
MultiStack also requires the bypass valve to be sized for a minimum flowrates of 280gpm without clarifying the corresponding max. pressure drop thru the valve, do you typically size it for a 3~5psi pressure drop? if not, how do you typically size this fast acting bypass control valve (MultiStack requires this valve to open fully within 60 seconds or less)?
[highlight #FCE94F]Bypass loop volume (Includes piping between V1 & chiller): 340 Gallons
Note: the bypass loop should be designed for a minimum of a 2 minute loop at all conditions. To obtain ensure the above volume is met.
Thank you,
Jo
I'm working on a chiller plant replacement project involving the installation of two (2) 180-ton each MultiStack MagLev water cooled chillers (one on standby) that has a designed flowrate of 373gpm thru each chiller. MultiStack has included in their submittal the following requirements (see below) concerning the minimum chilled water flowrates(187gpm) thru the chiller as well as the required minimum (340 Gallons) chilled water bypass loop volume. Have you seen this before, what's the reason for the 2-minute minimum volume in the bypass loop? The building's existing chilled water bypass pipe is located within the chiller mechanical room, we would have to add a chilled water bypass pipe much further downstream of the chilled water pumps to achieve the 340 gallons requirements if there is good reason to it. What's your thought on this?
Also, does the minimum required chilled water flowrate of 187gpm thru the chiller sound correct to you for chiller with design flowrate of 373gpm?
MultiStack also requires the bypass valve to be sized for a minimum flowrates of 280gpm without clarifying the corresponding max. pressure drop thru the valve, do you typically size it for a 3~5psi pressure drop? if not, how do you typically size this fast acting bypass control valve (MultiStack requires this valve to open fully within 60 seconds or less)?
[highlight #FCE94F]Bypass loop volume (Includes piping between V1 & chiller): 340 Gallons
Note: the bypass loop should be designed for a minimum of a 2 minute loop at all conditions. To obtain ensure the above volume is met.
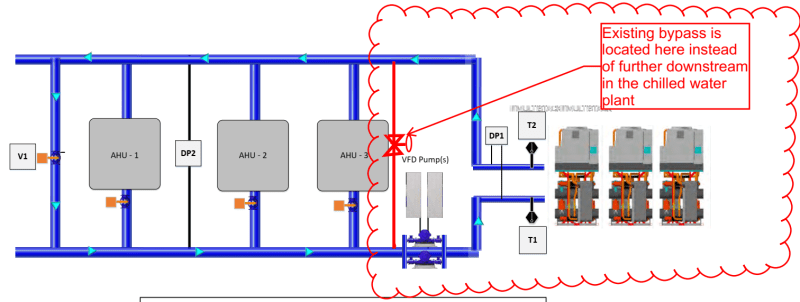
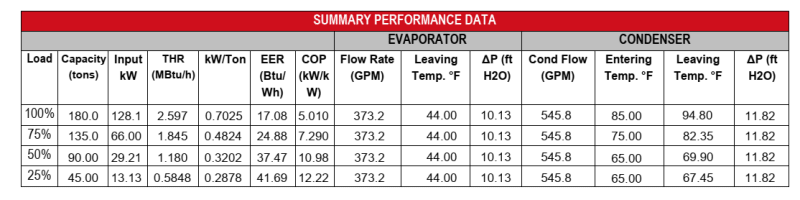
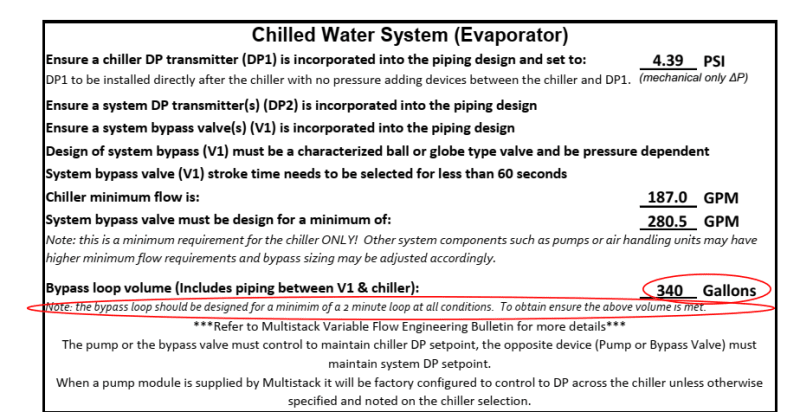
Thank you,
Jo