sendithard
Industrial
I'm having to program dimensions like this weekly. I'm not sure I've seen these type tangent to tangent dimensions in the standard, but whatever...assume it is a +-.005 here. They are a pain in the azz to make in GOM. I have two methods. Do you find the min/max of the actual features created(cylinders here), or do you find the min/max of the actual surfaces?....oh and this dimension has no datums so what is the setup you use to perform this measurment? Features would be a gage pin fit, ring gage fit, and do the math, surfaces would more surface profile distance. I ask myself what are they looking for with a tangent to tangent distance callout? Is this ASME Y14.5 acceptable, as it is an ambiguous callout from my point of view?
Then I think...why not use this type of callout to instruct for min wall thickness, instead of doing the LMC deal on the feature or the datum.
Then I think...why not use this type of callout to instruct for min wall thickness, instead of doing the LMC deal on the feature or the datum.
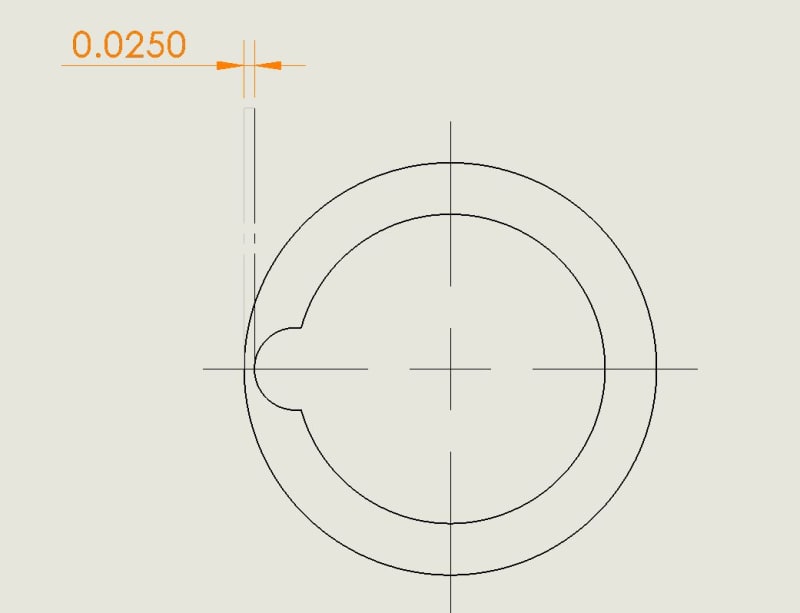