Hi All,
I am using an Accuenergy Data Acquisition Server ( to log data from a number of power meters. Each of the power meters communicates with the Accuenergy via Modbus RTU. I am having trouble getting the Accuenergy to poll data from an EATON IQ100 meter. A snapshot of the Modus Map for the EATON Meter is below. Theses are the three parameters that I am trying to poll.
I am new to Modbus (I'm an electrician) and I think I might be setting up the Modbus template wrong. In setting up the template the Acculink logger. The UI requires the following:
For Function, I select "Read_Holding REGISTERS" As I believe the power meter Modbus map uses Holding Registers only. I then enter 0383 as the starting address and in "Count", I enter 6. The UI then asks for the following:
To read "Watts, 3-Ph total" i enter the address 0383 and in multiplier the number 1. Does this seem correct so far? Unfortunately I can'f seem to make it work... I have also attached the full modbus map for the EATON meter in case I am missing somethig.
I am using an Accuenergy Data Acquisition Server ( to log data from a number of power meters. Each of the power meters communicates with the Accuenergy via Modbus RTU. I am having trouble getting the Accuenergy to poll data from an EATON IQ100 meter. A snapshot of the Modus Map for the EATON Meter is below. Theses are the three parameters that I am trying to poll.

I am new to Modbus (I'm an electrician) and I think I might be setting up the Modbus template wrong. In setting up the template the Acculink logger. The UI requires the following:
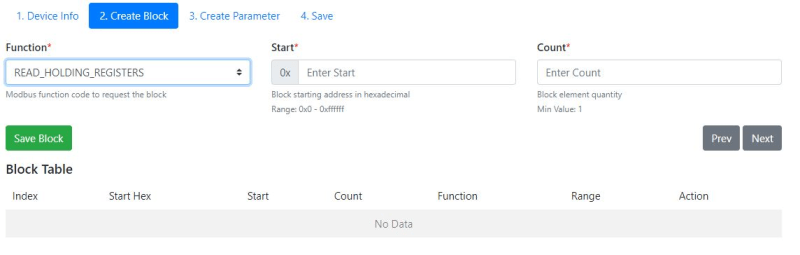
For Function, I select "Read_Holding REGISTERS" As I believe the power meter Modbus map uses Holding Registers only. I then enter 0383 as the starting address and in "Count", I enter 6. The UI then asks for the following:

To read "Watts, 3-Ph total" i enter the address 0383 and in multiplier the number 1. Does this seem correct so far? Unfortunately I can'f seem to make it work... I have also attached the full modbus map for the EATON meter in case I am missing somethig.