-
1
- #1
Hello,
I am creating an Abaqus model of a steel girder that is made of parts with different thicknesses for the flanges and web. I am using shell elements. The girder is 100m long and comprises of three different sections with uniform flange and web thicknesses. I used merge instances to create join the sections of the girder and create the 100m. The webs merged well however the flanges have a gap since I am using shell elements. I used tie constraints to create a connection between the two flanges with different thicknesses. However, I was wondering if there was another way to model this are to produce trusted results. in the real structure, these sections are welded together.
Or is this way of modeling sufficient and adding constraints sufficient?
I am creating an Abaqus model of a steel girder that is made of parts with different thicknesses for the flanges and web. I am using shell elements. The girder is 100m long and comprises of three different sections with uniform flange and web thicknesses. I used merge instances to create join the sections of the girder and create the 100m. The webs merged well however the flanges have a gap since I am using shell elements. I used tie constraints to create a connection between the two flanges with different thicknesses. However, I was wondering if there was another way to model this are to produce trusted results. in the real structure, these sections are welded together.
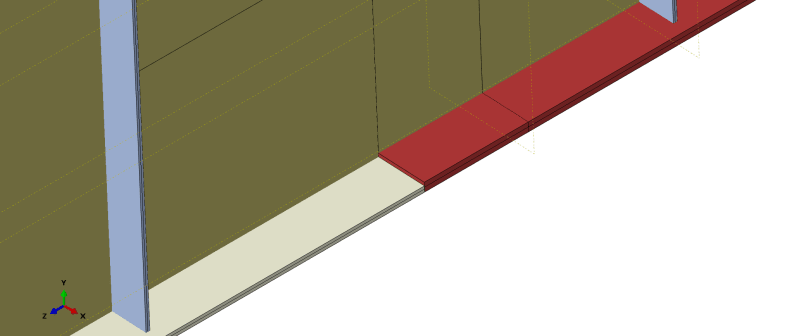
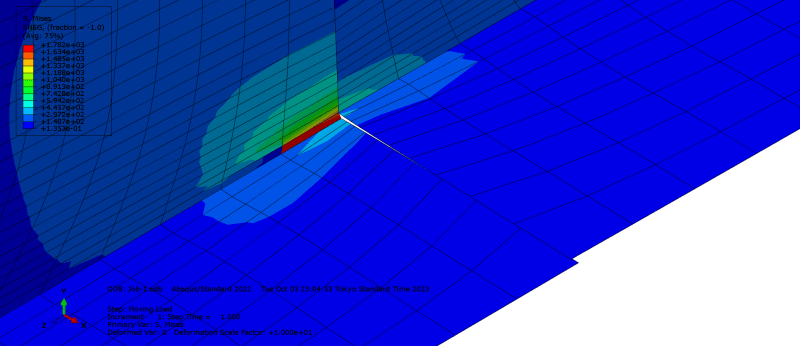
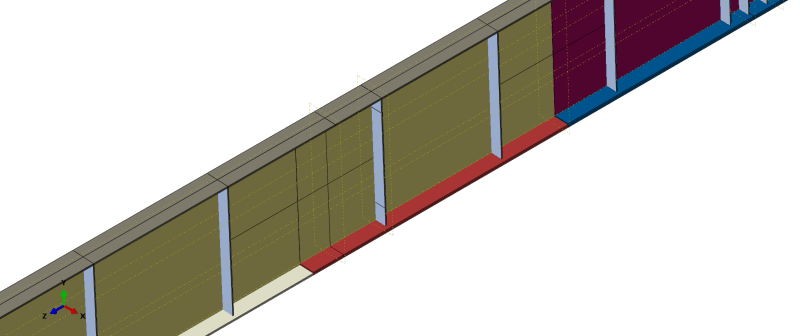
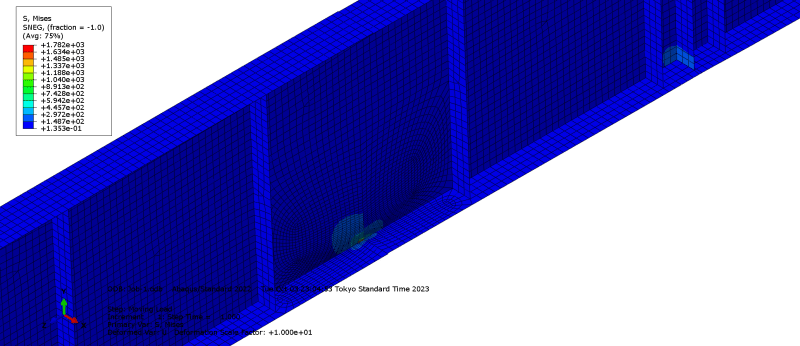
Or is this way of modeling sufficient and adding constraints sufficient?