Just wondering how you guys model walls that don't line up in 3D FE model like ETABS?
See below as an example. As you can see, the meshes that don't line up. And the slab meshes just match above. So, how do you normally separate the walls below into two or do you prefer manual meshing?
See below as an example. As you can see, the meshes that don't line up. And the slab meshes just match above. So, how do you normally separate the walls below into two or do you prefer manual meshing?
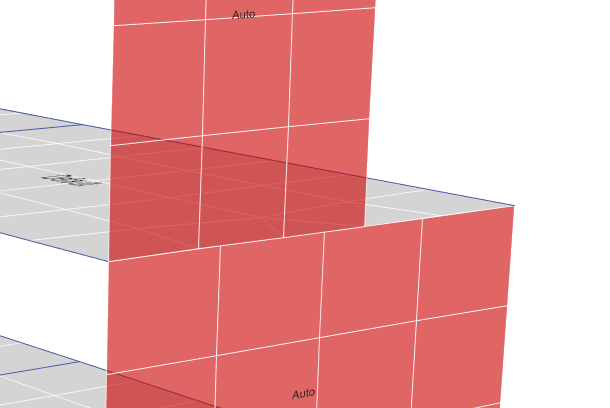
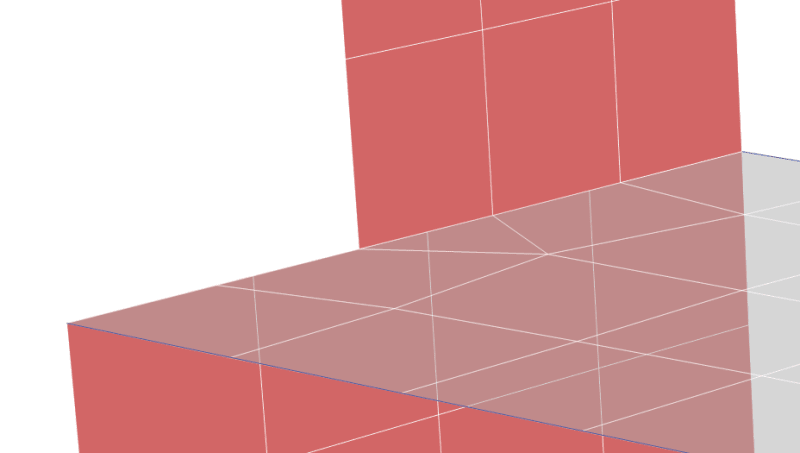