Forgot2Yield
Industrial
Hi all,
I wanted to get some opinions on the modifications I am planning on doing for an existing PEMB roof. This is related to another post I had on a PEMB roof addition (same project). I designed a new supporting structure and foundations for an additional enclosure sticking through the roof of an existing PEMB:
I am now in the process of designing some reinforcing for the existing building.
There is very little information available to me on this building so I have made a lot of assumptions when deciding how to reinforce around this opening in the PEMB.
There are two main items I am adding but I am getting pushback on one of these items and wanted to get some outside opinions:
Item 1)
I plan to reinforce all the existing purlins around the structure for additional snow drift. Even though the ground snow load for this area is only 5psf, I believe the snow drift will be significant enough around this structure ~60psf max. I plan to use bolted or welded C channel or angle or both
Item 2) (the one I am getting pushback on)
I assume that even though the eave struts in PEMB transfer most of the lateral load to the LRFS, there will still be some possible axial loads in those purlins that are being taken out that needs to be accounted for. I figure that since the extra load would be transferred to the purlins on each side of the opening, I need to add some reinforcing members between the frames there to account for this excess load that would otherwise fall on the existing eave strut and other purlins
In order to transfer this load I would also have to make that main frame much stiffer in weak axis bending so it could actually attract this load and transfer it to the outer reinforcement because I believe as it is the frame is probably so weak in out of plane bending that it would not be attracting that load. So in essence I am making a stiff box around this opening that will hopefully attract any load that the removed purlins would have been taking
I have been told that this second item seems unnecessary, but I am planning on doing a rough model to see if I am justified in this. Can I get some opinions on whether this seems necessary to do? I must note that there are no building drawings for this building, and there are no complete models. There is also no intent by anyone involved in this project to have a full model of the building created to check these modifications.
I wanted to get some opinions on the modifications I am planning on doing for an existing PEMB roof. This is related to another post I had on a PEMB roof addition (same project). I designed a new supporting structure and foundations for an additional enclosure sticking through the roof of an existing PEMB:
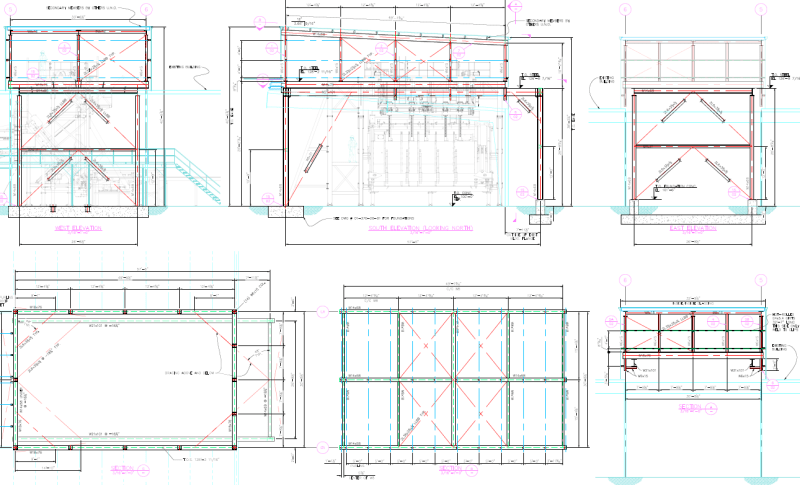
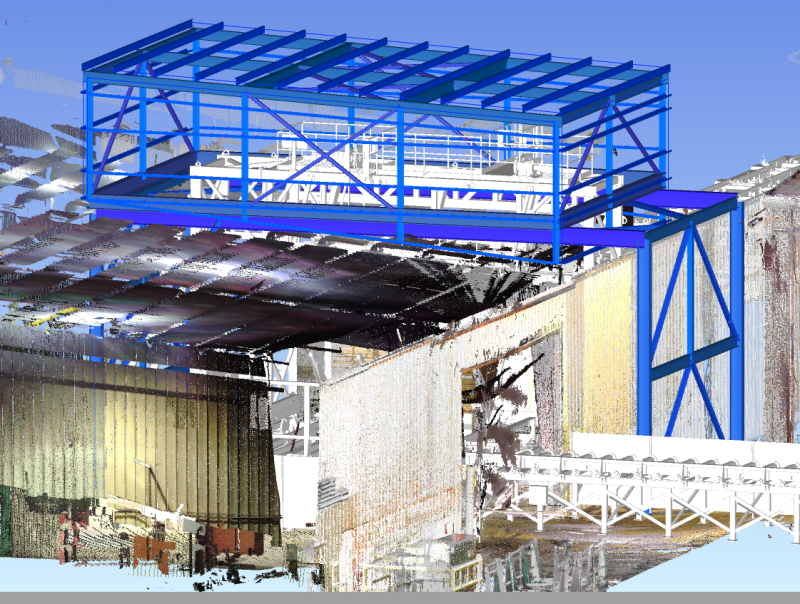
I am now in the process of designing some reinforcing for the existing building.
There is very little information available to me on this building so I have made a lot of assumptions when deciding how to reinforce around this opening in the PEMB.
There are two main items I am adding but I am getting pushback on one of these items and wanted to get some outside opinions:
Item 1)
I plan to reinforce all the existing purlins around the structure for additional snow drift. Even though the ground snow load for this area is only 5psf, I believe the snow drift will be significant enough around this structure ~60psf max. I plan to use bolted or welded C channel or angle or both
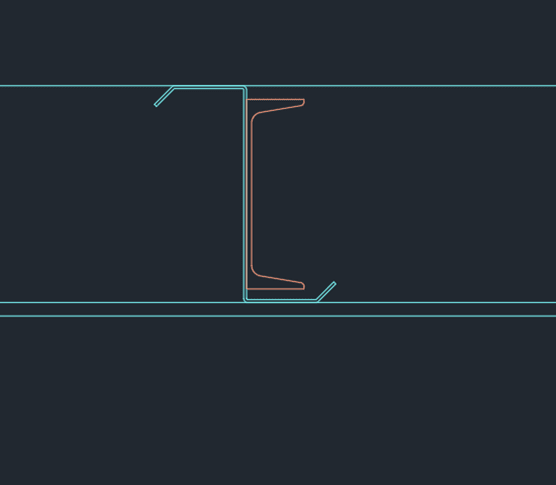
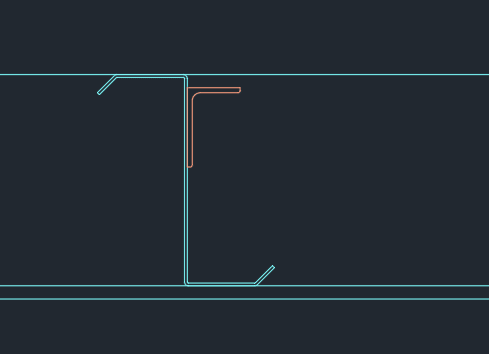
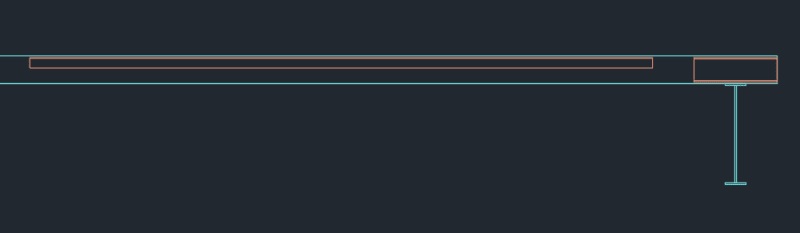
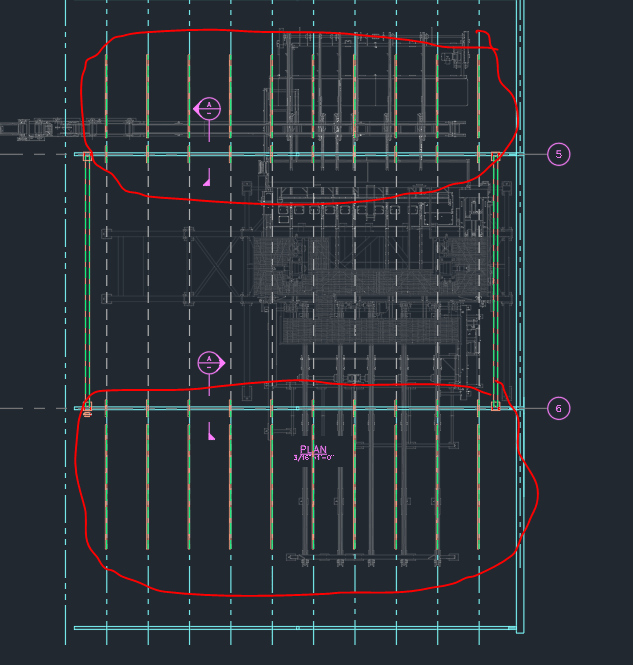
Item 2) (the one I am getting pushback on)
I assume that even though the eave struts in PEMB transfer most of the lateral load to the LRFS, there will still be some possible axial loads in those purlins that are being taken out that needs to be accounted for. I figure that since the extra load would be transferred to the purlins on each side of the opening, I need to add some reinforcing members between the frames there to account for this excess load that would otherwise fall on the existing eave strut and other purlins
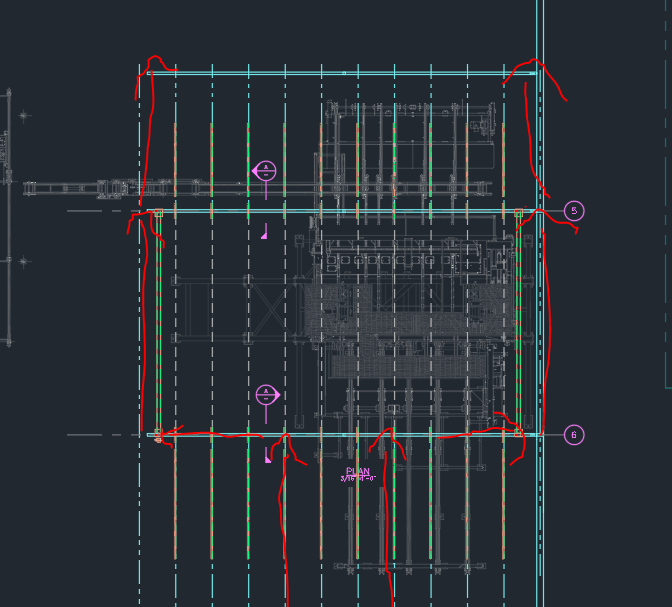
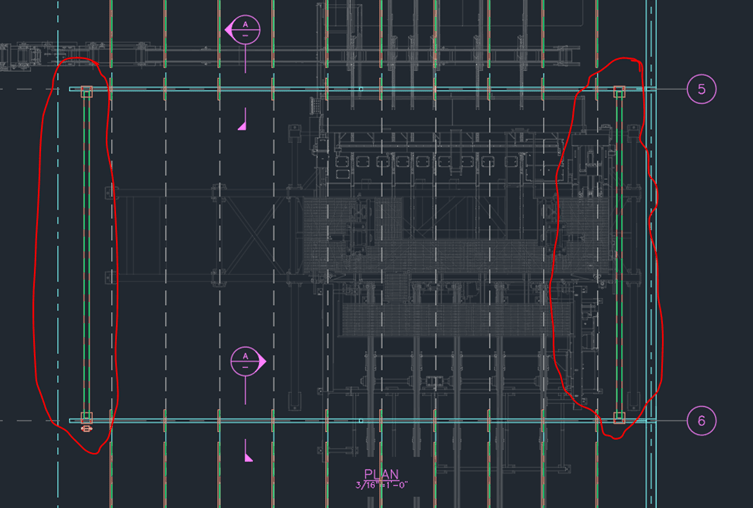
In order to transfer this load I would also have to make that main frame much stiffer in weak axis bending so it could actually attract this load and transfer it to the outer reinforcement because I believe as it is the frame is probably so weak in out of plane bending that it would not be attracting that load. So in essence I am making a stiff box around this opening that will hopefully attract any load that the removed purlins would have been taking
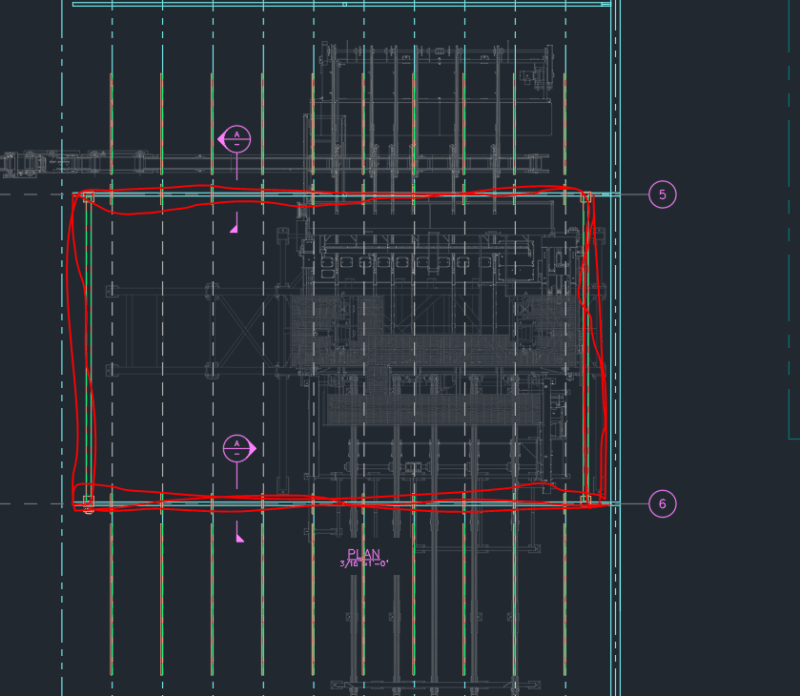
I have been told that this second item seems unnecessary, but I am planning on doing a rough model to see if I am justified in this. Can I get some opinions on whether this seems necessary to do? I must note that there are no building drawings for this building, and there are no complete models. There is also no intent by anyone involved in this project to have a full model of the building created to check these modifications.