I have a condition where I need to add a cantilever connection to an existing girder.
I'm unable to find a lot of literature on the type of moment connection I will need and the best way to analyze it.
I am using a welded end plate connection member which will bolted to the existing girder.
Existing steel is historic so using Fy = 30 ksi but the new beam will be 50 ksi. Also rules out a welded connection as an option unless we do some testing and analysis.
The existing steel will be retrofitted with cover plates to ensure it can handle the moment demand (~1600 kip-ft).
The main issue I see is the connection will have a lot more bolts in the web than the flanges and I wanted to see if I could include those web bolts to resist the moment demand.
Typically the flanges are assumed to carry the moment but it would be difficult to get enough bolts in the flanges to resist that demand.
I'm unable to find a lot of literature on the type of moment connection I will need and the best way to analyze it.
I am using a welded end plate connection member which will bolted to the existing girder.
Existing steel is historic so using Fy = 30 ksi but the new beam will be 50 ksi. Also rules out a welded connection as an option unless we do some testing and analysis.
The existing steel will be retrofitted with cover plates to ensure it can handle the moment demand (~1600 kip-ft).
The main issue I see is the connection will have a lot more bolts in the web than the flanges and I wanted to see if I could include those web bolts to resist the moment demand.
Typically the flanges are assumed to carry the moment but it would be difficult to get enough bolts in the flanges to resist that demand.
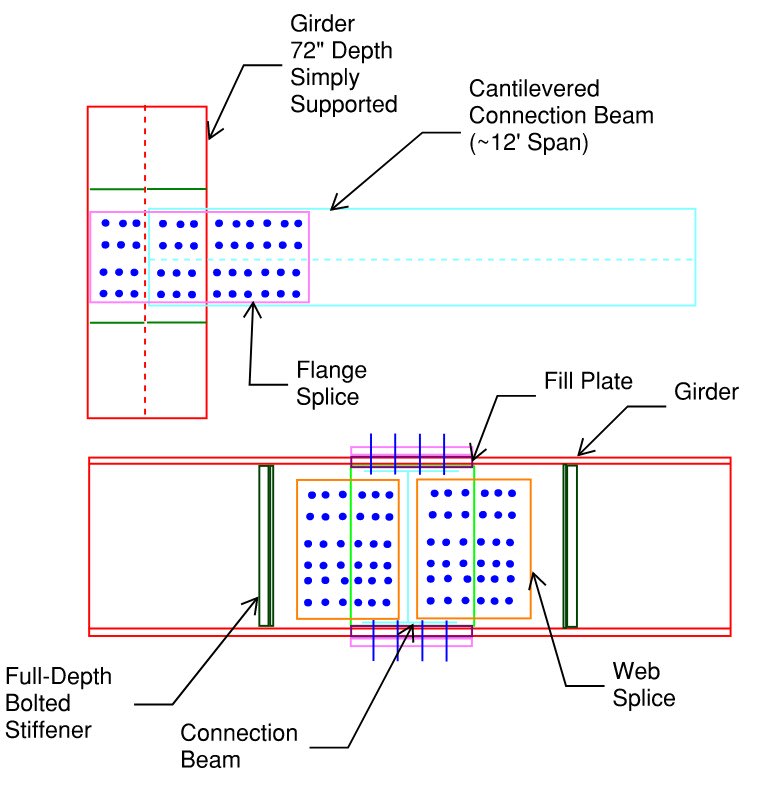