RabitPete
Structural
- Nov 24, 2020
- 109
Any recommendations/references on how to calculate capacity for one of the connections pictured below or any better ways to design a connection between 6 x 6 x 1/4 HSS column and W6-15 beam for a full moment? With a beam height of only 6" and only a couple inches to spare under the beam, the best solution I found so far was a column with an end plate and a beam bolted on top of it, but it is still no match for a full moment capacity of the column.
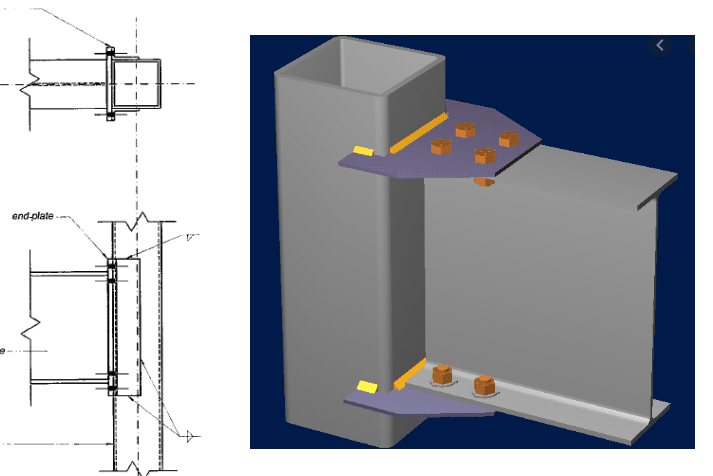