MegaStructures
Structural
Would you consider this a moment connection, or pinned connection if the following is true:
1. The connection between the HSS and I-beam is a direct weld (rather than a bolted cap plate as shown)
2. Instead of a continuous beam this is at a "corner" where two beams frame into each-other at a 90° angle and are welded together at the flanges
If not, would you then consider it a moment connection if there were a gusset plate welded to the HSS and bottom flange of the I-beam?
Edit: Of course there will be moment transferred by the HSS end connection, so I am asking about the rotational limit of the I-beams
“Any idiot can build a bridge that stands, but it takes an engineer to build a bridge that barely stands.”
1. The connection between the HSS and I-beam is a direct weld (rather than a bolted cap plate as shown)
2. Instead of a continuous beam this is at a "corner" where two beams frame into each-other at a 90° angle and are welded together at the flanges
If not, would you then consider it a moment connection if there were a gusset plate welded to the HSS and bottom flange of the I-beam?
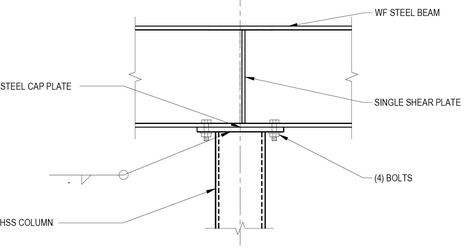
Edit: Of course there will be moment transferred by the HSS end connection, so I am asking about the rotational limit of the I-beams
“Any idiot can build a bridge that stands, but it takes an engineer to build a bridge that barely stands.”