Trainee339
Structural
- Jun 3, 2020
- 14
Hi All,
I am designing the moment resisting bracket for cold formed steel stud wall. I calculate the base moment and reaction and calculate the shear forces in the bolts connected to the stud (Bolt Pattern Force Distribution). and similarly used hilti profis to check the bolt capacity. My question is if I use the two bracket (as shown in the attached sketch would it be same? any cons of using 2 brackets instead of 1?
Need your thoughts.
I am designing the moment resisting bracket for cold formed steel stud wall. I calculate the base moment and reaction and calculate the shear forces in the bolts connected to the stud (Bolt Pattern Force Distribution). and similarly used hilti profis to check the bolt capacity. My question is if I use the two bracket (as shown in the attached sketch would it be same? any cons of using 2 brackets instead of 1?
Need your thoughts.
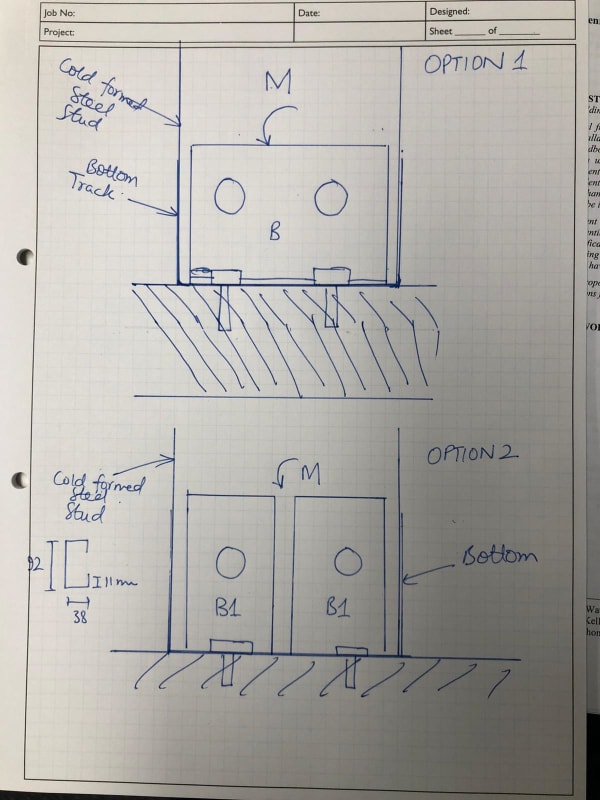