I have gotten pretty good with Solidworks over the past couple of days, especially since I figured out how to make parts mate. I had posted a thread earlier in the week requesting help with that.
Now, I have built a machine and it has probably a dozen or more parts. I have had pretty good luck so far with the mating process, but there are still a couple of areas I can't seem to grasp.
Here is one scenario:
I seem to do okay with mates as long as I have a reference point. For example, if I want to put a part directly down in the middle of a table, it easily mates when I select the bottom of the part and the top of the table. But, how do I put it in a certain place on that table (like the X and Y)? The only way I have figured out how to do this is to go back to the part file itself, create a sketch on the solid surface (for instance the table's top), and create what I call a footprint. I can usually put that footprint where I need it to be because I can dimension off of the edges of the table edges and get it there. Then, I go back to the part in the assembly, and when I mate the part, I simply grab one of the bottom edges of that part and line it up with one of the edges of the footprint. Then I do the other axis, whether it be X or Y. This lines the part up on the footprint and puts it where I need it to be.
I know there must be a correct way to do this. Am I doing it correctly or am I not?
Here is an example of what I am talking about. In this picture I have attached, you can see the parts there. The long part in the horizontal plane is called an idler arm. The part I am trying to mate (enclosed in the orange square wireframe) is the idler wheel mount. I have mated the back side of the mount to the idler arm. I have lined up the top edge of the mount to the top edge of the idler arm. No I am trying to move the mount to the right (maybe the X axis? - but if you look close at the axis thing at the bottom left of the picture it looks more like the Z axis) towards that light gray line. That light gray line is a sketch that I went back and added to the idler arm part as a reference point just for the operation I am trying to perform. It serves no other purpose.
When I try to mate this, I cannot select the light gray line like I was able to do on the base (which is the original part in the assembly and fixed). This is why I don't think this is the correct way to do this. The mount is not fixed, it is set at float.
Thanks!
Now, I have built a machine and it has probably a dozen or more parts. I have had pretty good luck so far with the mating process, but there are still a couple of areas I can't seem to grasp.
Here is one scenario:
I seem to do okay with mates as long as I have a reference point. For example, if I want to put a part directly down in the middle of a table, it easily mates when I select the bottom of the part and the top of the table. But, how do I put it in a certain place on that table (like the X and Y)? The only way I have figured out how to do this is to go back to the part file itself, create a sketch on the solid surface (for instance the table's top), and create what I call a footprint. I can usually put that footprint where I need it to be because I can dimension off of the edges of the table edges and get it there. Then, I go back to the part in the assembly, and when I mate the part, I simply grab one of the bottom edges of that part and line it up with one of the edges of the footprint. Then I do the other axis, whether it be X or Y. This lines the part up on the footprint and puts it where I need it to be.
I know there must be a correct way to do this. Am I doing it correctly or am I not?
Here is an example of what I am talking about. In this picture I have attached, you can see the parts there. The long part in the horizontal plane is called an idler arm. The part I am trying to mate (enclosed in the orange square wireframe) is the idler wheel mount. I have mated the back side of the mount to the idler arm. I have lined up the top edge of the mount to the top edge of the idler arm. No I am trying to move the mount to the right (maybe the X axis? - but if you look close at the axis thing at the bottom left of the picture it looks more like the Z axis) towards that light gray line. That light gray line is a sketch that I went back and added to the idler arm part as a reference point just for the operation I am trying to perform. It serves no other purpose.
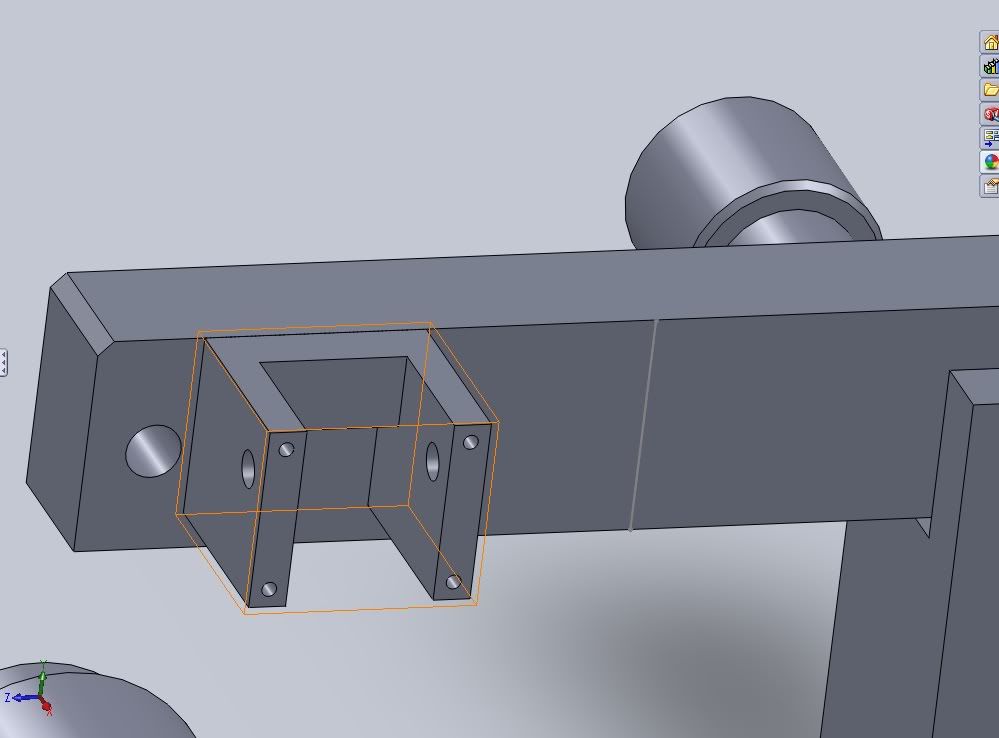
When I try to mate this, I cannot select the light gray line like I was able to do on the base (which is the original part in the assembly and fixed). This is why I don't think this is the correct way to do this. The mount is not fixed, it is set at float.
Thanks!