kissymoose
Structural
Check out this connection WSP came up with for a 66 story Manhattan skyscraper. They've got outriggers transferring vertical load into the core and horizontal trusses at the same location (they said some of the outrigger members are designed for 11,000 kips), coming in at varying angles to one point, so they decided the most economical thing would be to forge big ole cubes of steel to weld the members to. Some of those bad boys are probably around 3 tons by themselves.
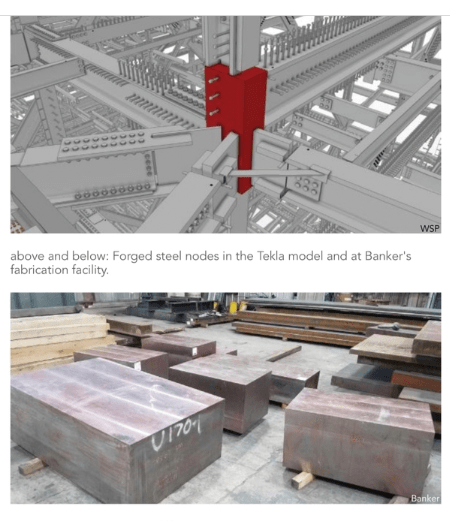
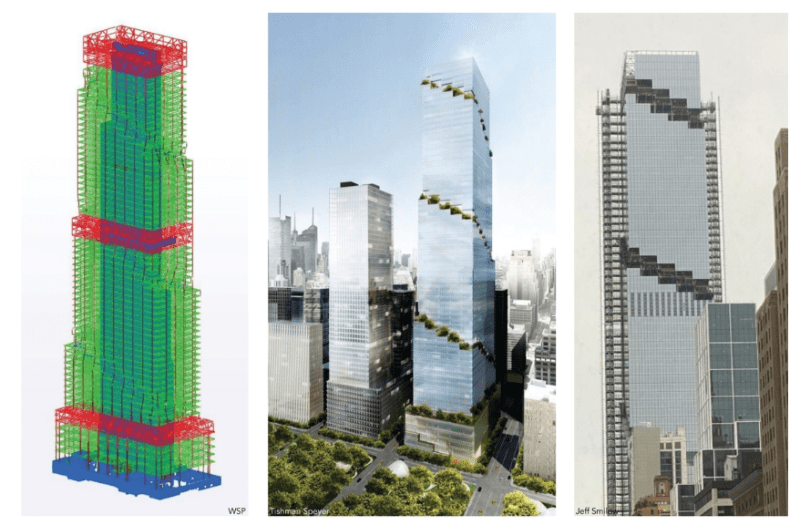