I was recently asked to do a motor starting study by the local utility for a 250hp vertical turbine pump. They are worried that the line voltage may sag more than 2% on startup, and if so, they may place restriction on time of day that it can be run. Now, I know enough in ETAP to be dangerous, and I was able to complete the majority of the study, but I don't have the confidence in my results that I would like.
The motor is connected to a Siemens voltage ramp soft starter.
My main question is, what kind of motor parameters are precisely required, and what parameters can be estimated? The nametag on the motor doesn't give too much more information besides HP, FLA, Voltage. Is it important that my model is accurate for X', X/R, Tdo, etc?
Trying to learn as much as possible.
Thanks.
The motor is connected to a Siemens voltage ramp soft starter.
My main question is, what kind of motor parameters are precisely required, and what parameters can be estimated? The nametag on the motor doesn't give too much more information besides HP, FLA, Voltage. Is it important that my model is accurate for X', X/R, Tdo, etc?
Trying to learn as much as possible.
Thanks.
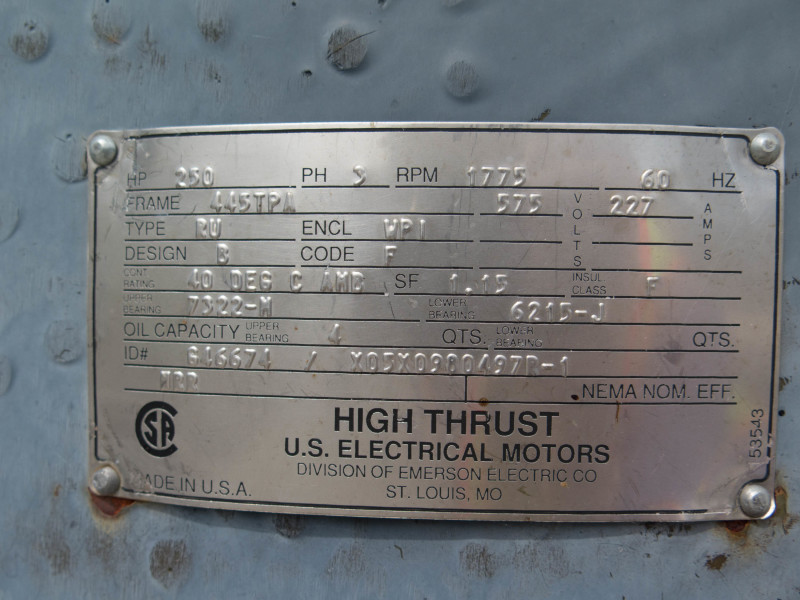
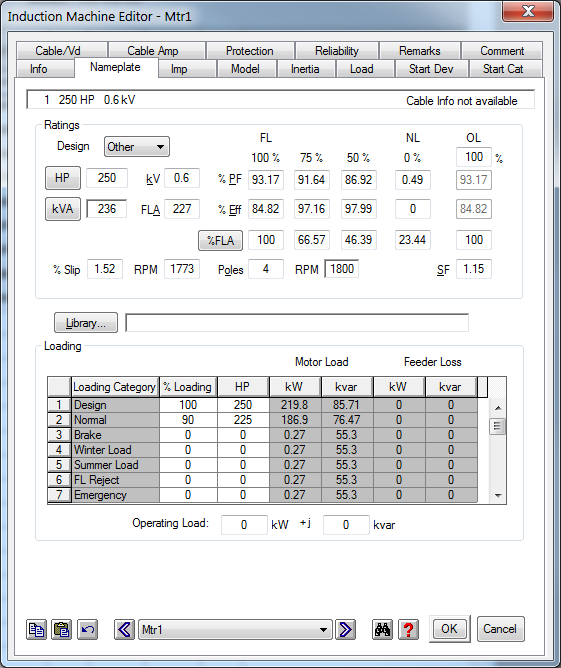
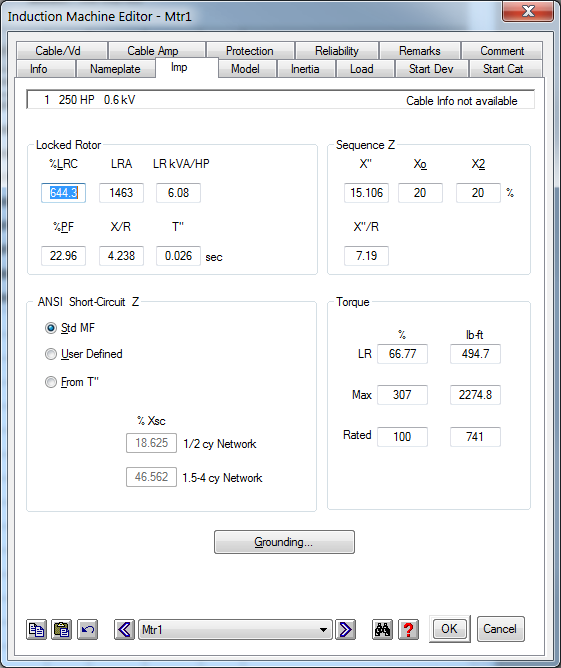
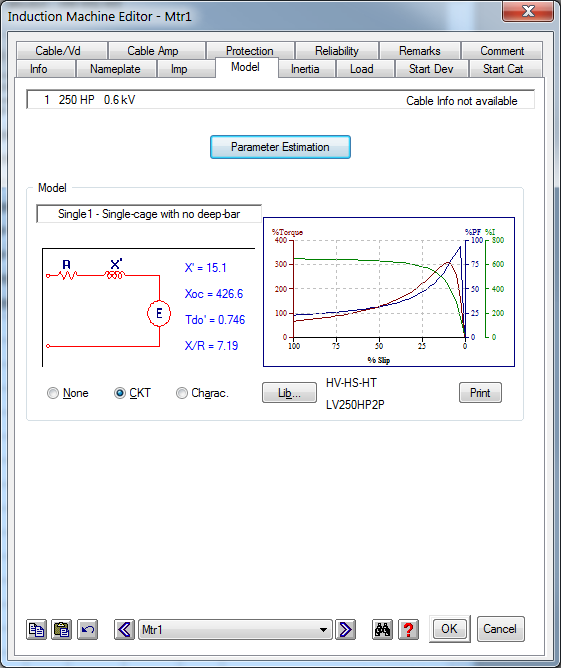