pv_mkk
Mechanical
- Jun 11, 2015
- 24
The reason is
1. The gasket at shell flange is broken and there is some vapor leakage when the media inside was heated.
2. It takes a long time to disconnect all piping and agitator on top of the vessel in order to replace a new gasket.
So my client would like to seal the gap between shell flange by welding plate inside of vessel around the shell flange gap as shown in the picture for temporary.
They will consider changing a new vessel in the future.
The vessel design condition is 25kPa@150C
Is the solution practical? or any advise would be appreciated.
1. The gasket at shell flange is broken and there is some vapor leakage when the media inside was heated.
2. It takes a long time to disconnect all piping and agitator on top of the vessel in order to replace a new gasket.
So my client would like to seal the gap between shell flange by welding plate inside of vessel around the shell flange gap as shown in the picture for temporary.
They will consider changing a new vessel in the future.
The vessel design condition is 25kPa@150C
Is the solution practical? or any advise would be appreciated.
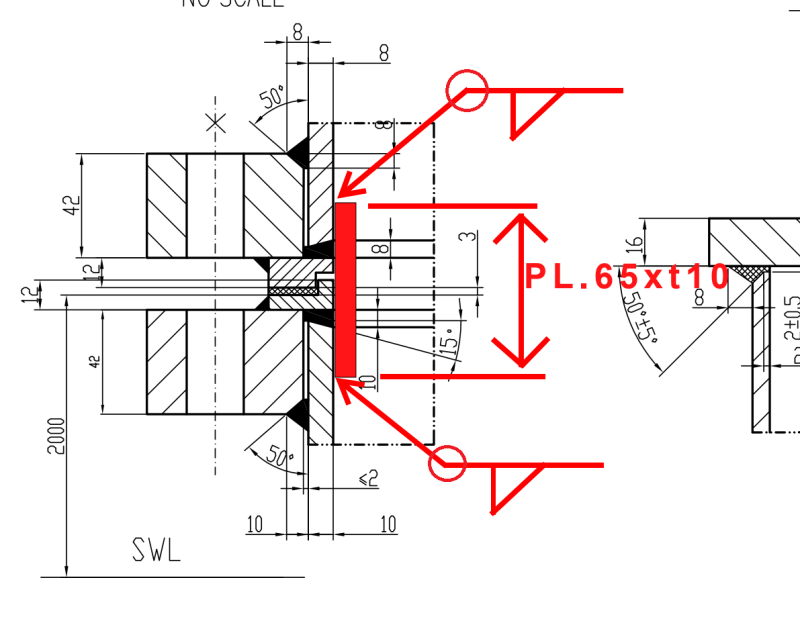