PJYDE
Aerospace
- Feb 26, 2018
- 20
Hi all,
Follow up on my previous thread Link and a closed thread Link.
I have a NAS6603-16 bolt and an AN365-1032 tension nut with this setup:
AN-960L thin washer: 0.03125"
Material: 0.95276"
AN960-10 washer: 0.06250"
Total: 1,04651"
The NAS6603-16 has a grip length of 1" and T (thread length) of 0.345".
After torquing the nut I have about 1.5 protruding threads.
So this joint respects these rules:
- 1 to max 3 washers
- no threads in material
- 1 to 3 protruding threads
- nut does not runout
The specification of NAS66 shows that there are max 2 incomplete threads between the grip and thread part of the bolt.
The nut does not runout of threads, it takes more than 1 full turn to runout of threads (measured without having the bolt installed).
What is your opinion about the "2 max incomplete threads"?
(it could be that the first part of the nut is in the incomplete thread part of the bolt)
Many thanks for your advice!
Follow up on my previous thread Link and a closed thread Link.
I have a NAS6603-16 bolt and an AN365-1032 tension nut with this setup:
AN-960L thin washer: 0.03125"
Material: 0.95276"
AN960-10 washer: 0.06250"
Total: 1,04651"
The NAS6603-16 has a grip length of 1" and T (thread length) of 0.345".
After torquing the nut I have about 1.5 protruding threads.
So this joint respects these rules:
- 1 to max 3 washers
- no threads in material
- 1 to 3 protruding threads
- nut does not runout
The specification of NAS66 shows that there are max 2 incomplete threads between the grip and thread part of the bolt.
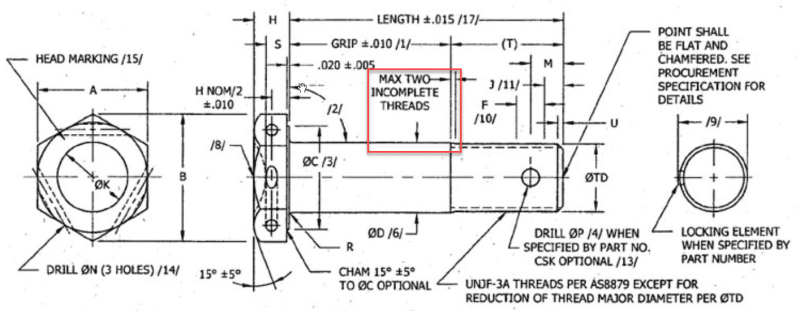
The nut does not runout of threads, it takes more than 1 full turn to runout of threads (measured without having the bolt installed).
What is your opinion about the "2 max incomplete threads"?
(it could be that the first part of the nut is in the incomplete thread part of the bolt)
Many thanks for your advice!