I have two simple links that I need to couple. The links nest together tightly plus the angle of rotation of the links is small and any rotation is occasional/very slow like you would find in a hinge. The major static force on the 12mm pin will be approximately 200 pounds in linear tension (first cut thinking).
There are two goals for the fastener:
1. Since axial forces driving the pin out are minimal, a standard bolt/nut is a bit of mechanical overkill, leaves projections on both sides that are unwanted and requires more assembly time than desirable.
2. The links are 6061 aluminum and the atmosphere has exposure to occasional salt moisture and vapor. So fastener corrosion has to be precluded by the material chosen.
A thin-head, grooved pin with an eClip was the first to come to mind. While this method is a solid solution and better than a bolt/lock nut, I am wondering if anyone has ever seen a pin with with some nature of expanded end that would compress during insertion, then open on the other side to 'reliably' lock itself in place with one insertion motion to drive fastener cost and labor to a minimum?
(Or maybe some form of rivet forming design that also did not require a second part to be purchased/handled ... and had the added advantage over an eClip or push clip that some random debris could pop it off.)
All comments, suggestions and especially even better ideas are most welcome!
Best regards,
B
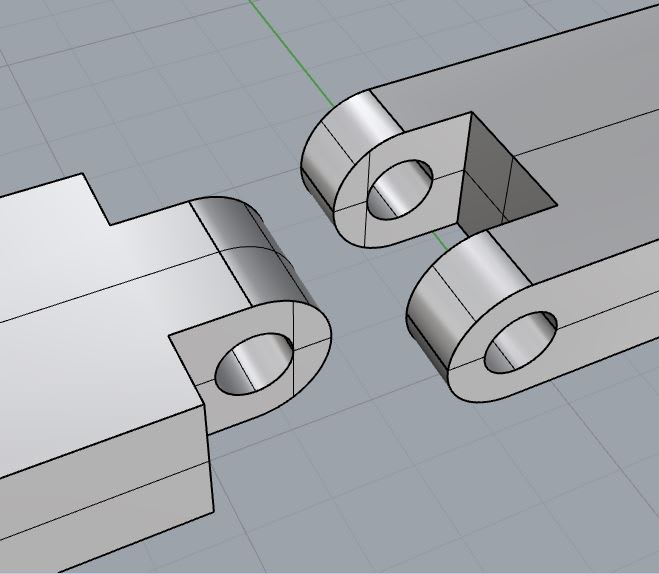
There are two goals for the fastener:
1. Since axial forces driving the pin out are minimal, a standard bolt/nut is a bit of mechanical overkill, leaves projections on both sides that are unwanted and requires more assembly time than desirable.
2. The links are 6061 aluminum and the atmosphere has exposure to occasional salt moisture and vapor. So fastener corrosion has to be precluded by the material chosen.
A thin-head, grooved pin with an eClip was the first to come to mind. While this method is a solid solution and better than a bolt/lock nut, I am wondering if anyone has ever seen a pin with with some nature of expanded end that would compress during insertion, then open on the other side to 'reliably' lock itself in place with one insertion motion to drive fastener cost and labor to a minimum?
(Or maybe some form of rivet forming design that also did not require a second part to be purchased/handled ... and had the added advantage over an eClip or push clip that some random debris could pop it off.)
All comments, suggestions and especially even better ideas are most welcome!
Best regards,
B