Mr_Curious
Mechanical
Hi everyone
.
I am making stress analysis of an electric motor.
The problem is i have gotten the higest stress near the weld connection which is the reason why my construction is not satisfied the required safety factor.
The highest stress is situated at one fourth of the part depth (third picture) so i suppose if i calculate this cut by hand i will get much lower result.
I have no idea how i can try to reduce the stress. Currently i am changing the grid and if it wont help and i dont know what to do else.
Can someone advice me on what else i can do to reduce the stress at this spot?
Thanks in advance.
![[smile] [smile] [smile]](/data/assets/smilies/smile.gif)
I am making stress analysis of an electric motor.
The problem is i have gotten the higest stress near the weld connection which is the reason why my construction is not satisfied the required safety factor.
The highest stress is situated at one fourth of the part depth (third picture) so i suppose if i calculate this cut by hand i will get much lower result.
I have no idea how i can try to reduce the stress. Currently i am changing the grid and if it wont help and i dont know what to do else.
Can someone advice me on what else i can do to reduce the stress at this spot?
Thanks in advance.
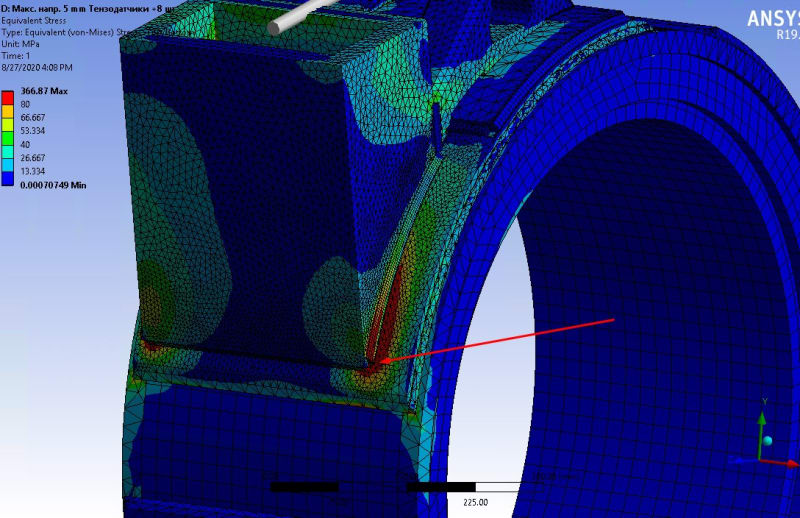
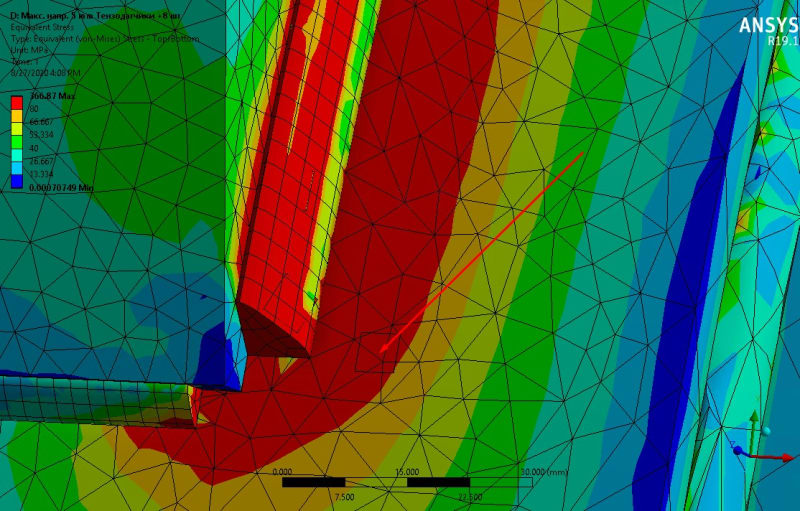
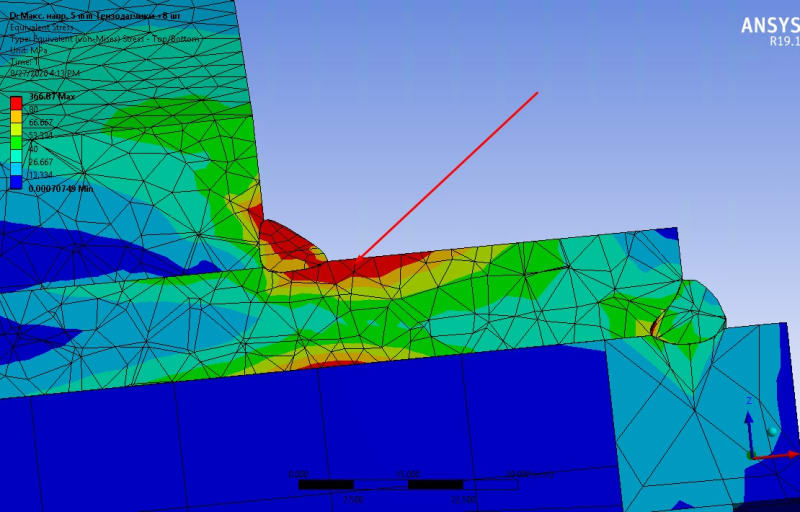