Hello everyone. I am a civil engineer by education, however, I have a side business that manfactures amateur and professional camera mounts.
My professional camera mount, called the Pro-Mount, is used by professional videographers to videotape from within trees (i.e., whitetail deer and bear hunts for the Outdoor Channel, Sportsman Channel, ESPN Outdoors, etc.).
My Pro-Mount is able to level vertically and horizontally. I am trying to redesign the "shoulder joint" which provides the horizontal leveling. Please see the pictures below.
Currently, the shoulder joint is two 3 inch diameter plates. The front plate has two slots with two 3/8" hex bolts passing through the slots and into keenserts located in the back plate. There is a stainless steel 1/2" diameter shaft extending through the center of both plates.
My problem is that when the arms are fully extended 90 degrees to the tree (and in line with the rotation of the shoulder joint), the joint can slip. Obviously slipping is dependent upon the force applied to the two bolts and the load applied to the end of the arm. Altough the TV type cameras weigh about 30 to 40 pounds, I would like the arm to be able to handle about 80 lbs without slipping. Additionally, I would like to incorporate a handle in place of the allen bolts so the user doesn't have to carry an allen wrench. Doing this reduces the amount of force the user can place on the bolts.
Is there a book out there that might help us design this joint to maximize the clamping effort?
By the way, we can't increase the diameter of the two plates and the two materials must be aluminum. Additionally, the joint must provide enough rotation to allow leveling (say minimum of 15 degree each direction).
Thanks for your help,
Darren
My professional camera mount, called the Pro-Mount, is used by professional videographers to videotape from within trees (i.e., whitetail deer and bear hunts for the Outdoor Channel, Sportsman Channel, ESPN Outdoors, etc.).
My Pro-Mount is able to level vertically and horizontally. I am trying to redesign the "shoulder joint" which provides the horizontal leveling. Please see the pictures below.
Currently, the shoulder joint is two 3 inch diameter plates. The front plate has two slots with two 3/8" hex bolts passing through the slots and into keenserts located in the back plate. There is a stainless steel 1/2" diameter shaft extending through the center of both plates.
My problem is that when the arms are fully extended 90 degrees to the tree (and in line with the rotation of the shoulder joint), the joint can slip. Obviously slipping is dependent upon the force applied to the two bolts and the load applied to the end of the arm. Altough the TV type cameras weigh about 30 to 40 pounds, I would like the arm to be able to handle about 80 lbs without slipping. Additionally, I would like to incorporate a handle in place of the allen bolts so the user doesn't have to carry an allen wrench. Doing this reduces the amount of force the user can place on the bolts.
Is there a book out there that might help us design this joint to maximize the clamping effort?
By the way, we can't increase the diameter of the two plates and the two materials must be aluminum. Additionally, the joint must provide enough rotation to allow leveling (say minimum of 15 degree each direction).
Thanks for your help,
Darren
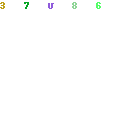
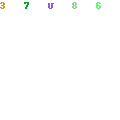
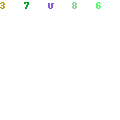