Hello,
I'm currenly working on a small project, i'm trying to figure out a mounting design for the tanks (pressure vessel) in an aircraft wings (to the ribs or skin), so that the pressure tanks could take some of the aerodynamic loads. The problem for me is the requirement, that the tanks could be easily disassembled and expansion of the tanks need to be accounted.
The image shows, the current structures that i'm working with, problem with the mounting at the root is already solved, but since the tanks is "hanging" inside the wings, a mounting structure that accounts for expansion and ease of dissasembly is needed, so that the tanks does not come to contact with the skin in flight. My ideas was just to place a rubber material under the bottom skin, and just let the tank come into contact with the skin. But i don't know how realistic this is. Any insights would be helpful
Thank You
I'm currenly working on a small project, i'm trying to figure out a mounting design for the tanks (pressure vessel) in an aircraft wings (to the ribs or skin), so that the pressure tanks could take some of the aerodynamic loads. The problem for me is the requirement, that the tanks could be easily disassembled and expansion of the tanks need to be accounted.
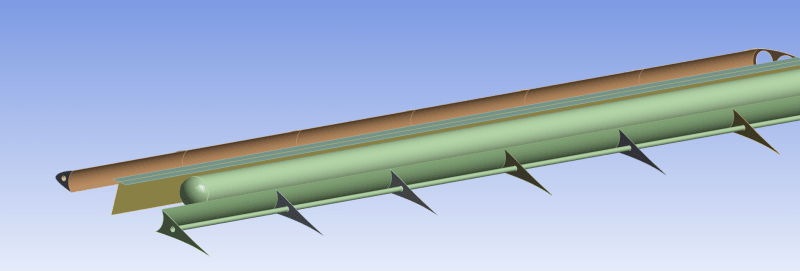
The image shows, the current structures that i'm working with, problem with the mounting at the root is already solved, but since the tanks is "hanging" inside the wings, a mounting structure that accounts for expansion and ease of dissasembly is needed, so that the tanks does not come to contact with the skin in flight. My ideas was just to place a rubber material under the bottom skin, and just let the tank come into contact with the skin. But i don't know how realistic this is. Any insights would be helpful

Thank You
