BeckSt
Structural
- Dec 29, 2019
- 4
It is my first time to design irregular 2 way slab and I need some help from you.
I have used FEA for the slab analysis and below is the shell stress. Most of the stress is less than 3 MPa. but I have noticed that the stress in some mesh is greater than 35MPa (the green ones). Why is that? Is it more because of the model error? (There is only UDL on the slab. no point load added)
Also. what books do you guys recommend for slab design? I am not very confident in arranging the reinforcement correctly. Can anyone provide some resource for irregular slab design example including the reo arrangement after analysis? Thank you very much.
I have used FEA for the slab analysis and below is the shell stress. Most of the stress is less than 3 MPa. but I have noticed that the stress in some mesh is greater than 35MPa (the green ones). Why is that? Is it more because of the model error? (There is only UDL on the slab. no point load added)
Also. what books do you guys recommend for slab design? I am not very confident in arranging the reinforcement correctly. Can anyone provide some resource for irregular slab design example including the reo arrangement after analysis? Thank you very much.
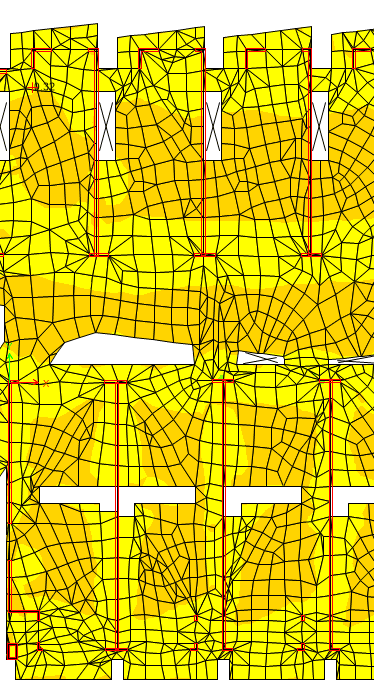
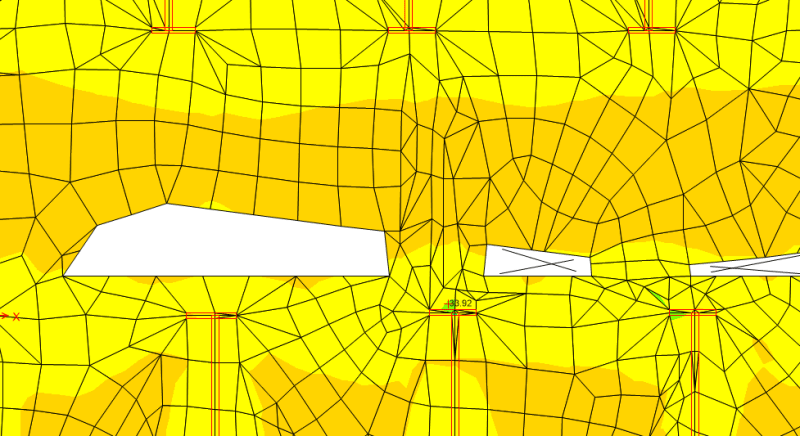