MECH-DESIGNER
Mechanical
Can I get someone to point me in the right direction? Here is my problem. I have a driveshaft that is inserted into a square tube and than plug welded perpendicular to the axis. I was wondering if someone knew of a formula to help predict this(torque/stress)? Currently there is no documentation on our current process and I'd like to better document it for any future changes.
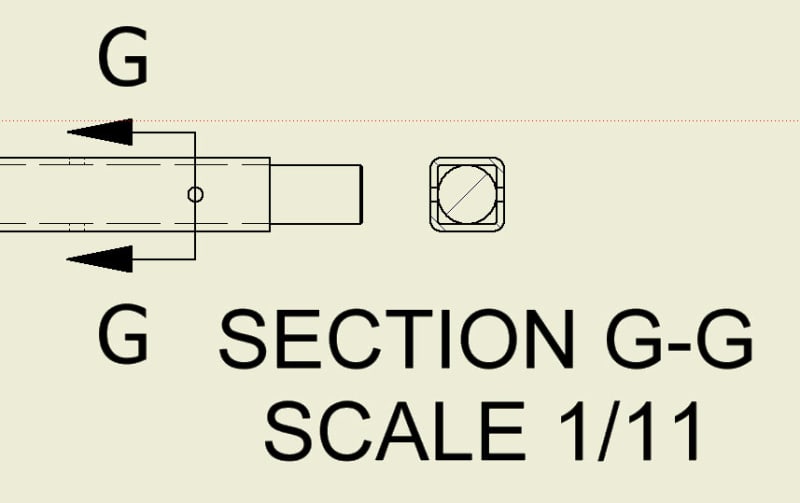