spagett
Aerospace
- Jan 18, 2021
- 4
Hi All,
I am a bit confused about the behavior of metal doubler reinforcing repairs for cutouts. Say I have a plate loaded in tension, the standard method of sizing the repair is to go 1 gauge thicker, and size the amount and type of fasteners / required doubler overlap needed based on the load capability removed as a result of the cutout.
For the sake of this conversation lets ignore the stiffness increase due to adding the doubler.
Without the reinforcement clearly the loadpath around the cutout is altered. Clearly the material above and below the cutout now has increased load.
Once the doubler is applied does the loadpath around the cutout return to a relatively unaltered state, or is there still some degree of bypass around the cutout?
For section AA there is a clear loadpath from the parent material into the doubler, but in for section BB how much load transfer would actually be transferred into the doubler (assuming same material, but 1 gauge thicker). It seems to me like section BB is not really a joint. The doubler is there, but what is it actually doing?
So at section BB if there is still bypass around the cutout, and the load does not transfer well into doubler then we should have a big concern about net tension in the parent material.
The doubler approach is very clearly time tested and very clearly works. But my question is how are these repairs not failing in net tension?
I am a bit confused about the behavior of metal doubler reinforcing repairs for cutouts. Say I have a plate loaded in tension, the standard method of sizing the repair is to go 1 gauge thicker, and size the amount and type of fasteners / required doubler overlap needed based on the load capability removed as a result of the cutout.
For the sake of this conversation lets ignore the stiffness increase due to adding the doubler.
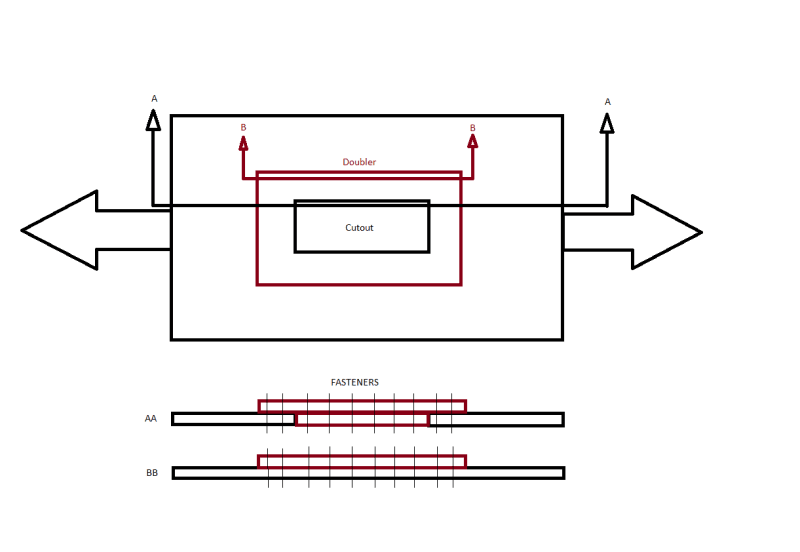
Without the reinforcement clearly the loadpath around the cutout is altered. Clearly the material above and below the cutout now has increased load.
Once the doubler is applied does the loadpath around the cutout return to a relatively unaltered state, or is there still some degree of bypass around the cutout?
For section AA there is a clear loadpath from the parent material into the doubler, but in for section BB how much load transfer would actually be transferred into the doubler (assuming same material, but 1 gauge thicker). It seems to me like section BB is not really a joint. The doubler is there, but what is it actually doing?
So at section BB if there is still bypass around the cutout, and the load does not transfer well into doubler then we should have a big concern about net tension in the parent material.
The doubler approach is very clearly time tested and very clearly works. But my question is how are these repairs not failing in net tension?