Yosemite_Sam
Electrical
Hello-
some much needed corrosion advice needed. These parts are from a water cooling assembly of a tool. Top and bottom platen, process cooling water of about 280kOhm-cm resistivity (RT to about 70C at most) that runs through these parts. Not pictured is the SS-made diverter that sits in between. The parts are said to have been Ni plated Aluminum. We were told that this problem would not have occurred had we employed a dedicated chiller with a an additive for the water. For whatever reason it wasn't done and now we have this growth. I haven't attempted sanding or chemical etch yet. Not sure if there is pitting.
If anyone can help with
a) how to identify what is corroding chemically
b) how to remove the growths with minimal damage to the surface itself
Much appreciated
some much needed corrosion advice needed. These parts are from a water cooling assembly of a tool. Top and bottom platen, process cooling water of about 280kOhm-cm resistivity (RT to about 70C at most) that runs through these parts. Not pictured is the SS-made diverter that sits in between. The parts are said to have been Ni plated Aluminum. We were told that this problem would not have occurred had we employed a dedicated chiller with a an additive for the water. For whatever reason it wasn't done and now we have this growth. I haven't attempted sanding or chemical etch yet. Not sure if there is pitting.
If anyone can help with
a) how to identify what is corroding chemically
b) how to remove the growths with minimal damage to the surface itself
Much appreciated
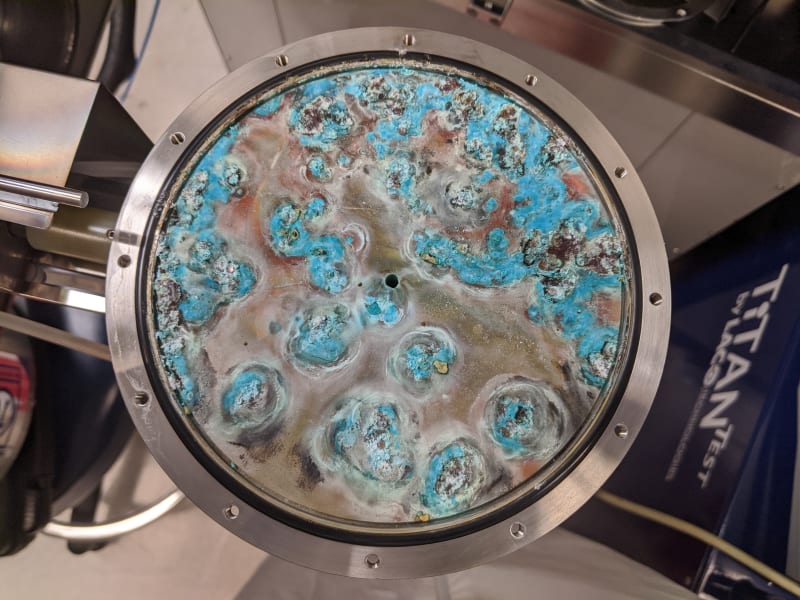
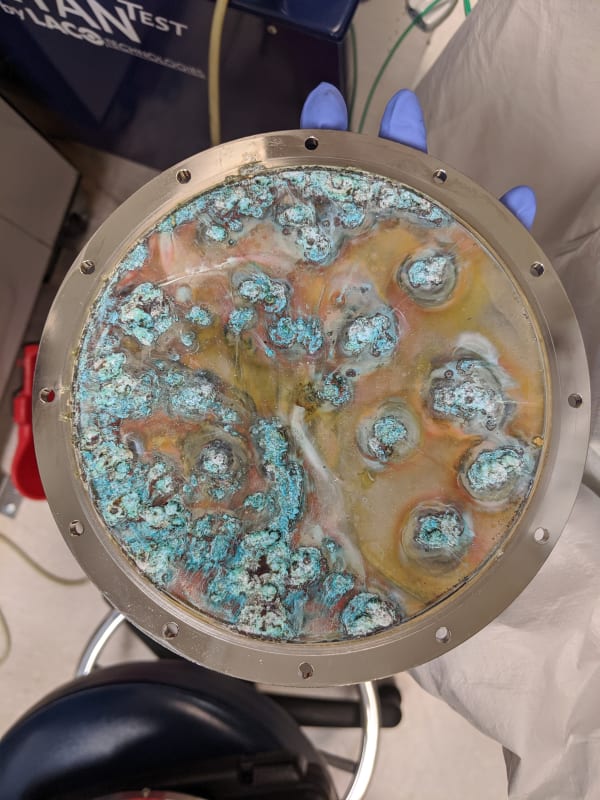