Doodler3D
Mechanical
- Jan 20, 2020
- 188
Hi,
For unknown reasons, I cant get reasonable values of nodal forces for a scoped entity along the base of a weld. Any advise on the use of ENFO APDL command?
Thank you.
For unknown reasons, I cant get reasonable values of nodal forces for a scoped entity along the base of a weld. Any advise on the use of ENFO APDL command?
Thank you.
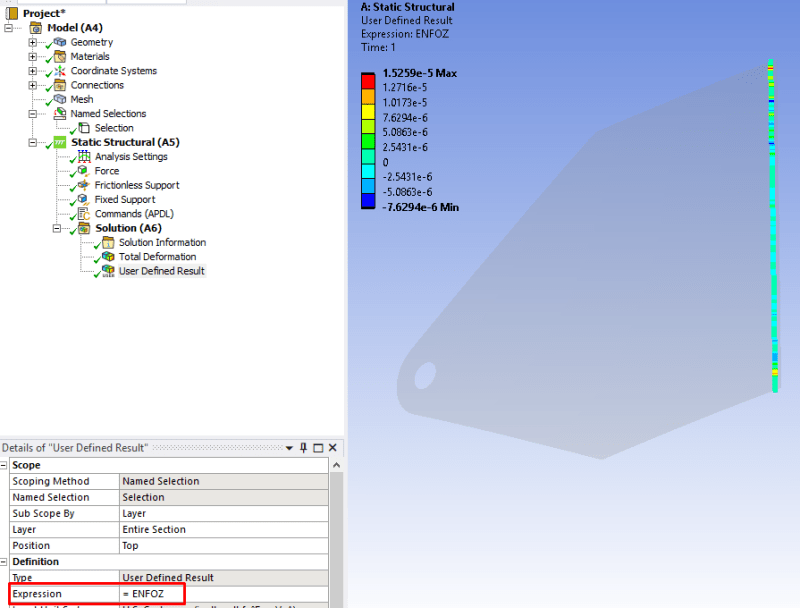