Nick7805
Mechanical
- Nov 19, 2021
- 21
I'm trying to model a silo with a hopper (shell elements) resting against the ground (solid elements) using Inventor Nastran. In my current model, the ground has significantly lower stiffness than the hopper base and there is a separation contact defined between them. There is also various offset bonded contacts set between components of the silo, however the ground/base separation contact by-far produces the most contact elements.
I'm having a lot of trouble getting convergence, even at very low load levels (0.01% total load). I've attached a picture of the model below for reference.
The model will run and produce good results as long as the ground isn't in the model. Only when I add the ground to the model, I have issues getting convergence. So far I've tried the following:
- Reducing the number of contacts in the model (reducing the activation distance for base/ground contact)
- Modifying the convergence criteria to not include the load
- Modifying the convergence criteria to start at a low load level and increasing the number of increments
- Reducing contact stiffness to 0.5
- Changing the contact type from separation to separation with no sliding, as very little sliding is expected
- Testing as a bonded contact -- the model runs and produces results as expected if the contact is set to bonded
Typically the convergence issue is with load (and to a lesser extent, work); displacement always has converged so far. Depending on the settings, the solution either diverges or reaches the maximum number of bisections permitted. I'm fairly inexperienced using FEA and I'm not sure what to do in order to diagnose and fix the problem. Does anyone have any suggestions?
I'm having a lot of trouble getting convergence, even at very low load levels (0.01% total load). I've attached a picture of the model below for reference.
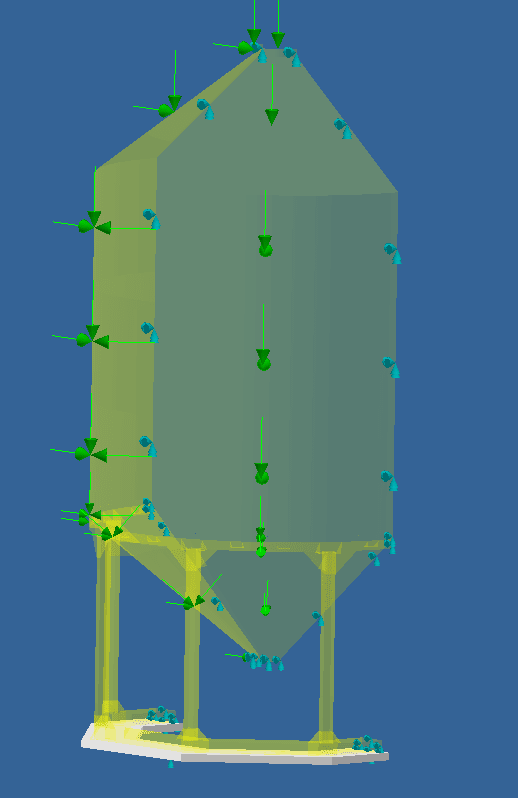
The model will run and produce good results as long as the ground isn't in the model. Only when I add the ground to the model, I have issues getting convergence. So far I've tried the following:
- Reducing the number of contacts in the model (reducing the activation distance for base/ground contact)
- Modifying the convergence criteria to not include the load
- Modifying the convergence criteria to start at a low load level and increasing the number of increments
- Reducing contact stiffness to 0.5
- Changing the contact type from separation to separation with no sliding, as very little sliding is expected
- Testing as a bonded contact -- the model runs and produces results as expected if the contact is set to bonded
Typically the convergence issue is with load (and to a lesser extent, work); displacement always has converged so far. Depending on the settings, the solution either diverges or reaches the maximum number of bisections permitted. I'm fairly inexperienced using FEA and I'm not sure what to do in order to diagnose and fix the problem. Does anyone have any suggestions?