moteor
Aerospace
- Jul 17, 2015
- 2
Hi everyone,
Thanks for the help in advance.
I have a project with a woodchipper to deisel engine build, with a woodchipper that is rated to 105 HP @ 540 RPM. I was wondering what the torque rating for the machine would be, whilst its being driven from a diesel engine?
I believe there is a direct relationship between Torque and Horspower from Engines;
TORQUE = HP x 5252 ÷ RPM
Therefore Torque = 1021 lb.ft or 1384.29 Nm
1) So I have done the math, but is that right? Is that really what the torque the machine can handle?
I also have the torque and HP stats of the engine as below:
I need to find the torque of the engine related by the rated torque capacity of the wood chipper = 1384.29 Nm. @540 RPM?
Also I need to find out what engine speed can provide the max torque rating for the machine as the engine has to be reduced by a ratio through pulleys to match the max RPM of the machine. My first question is:
2) Does reducing a gear ratio, say 3.7 : 1 multiply the torque by that much? So what would happen to the machine?
If;
Torque x gear ratio = torque at the wheel
Then @ 2000 RPM the engine would provide 169.1 Nm , therefore multiply by the 3.7037 times the motor is rotating faster than 540 RPM and you have the figure 625.92 which is under the figure we have for the rated capacity of the wood chipper.
3) At the moment I am working with this:
My plan is to have a compound pulley system with 3 groove vbelt pulleys rated to at least +20% over 105 HP.
I am looking at the 2 pulley sizes of 117.5 and 305.5 and being in a drive chain to have 2 of each.
they give a ratio of 2.6 : 1 so 2 of them is 2.6 x 2.6 = 6.76.
so at 3,650 RPM it will be reduced by 6.76 times giving 539.4 rpm. So this gives peak power at peak revs.
Please can you confirm if this is right or REALLY IS ALL IN MY HEAD!!
Thanks for the help in advance.
I have a project with a woodchipper to deisel engine build, with a woodchipper that is rated to 105 HP @ 540 RPM. I was wondering what the torque rating for the machine would be, whilst its being driven from a diesel engine?
I believe there is a direct relationship between Torque and Horspower from Engines;
TORQUE = HP x 5252 ÷ RPM
Therefore Torque = 1021 lb.ft or 1384.29 Nm
1) So I have done the math, but is that right? Is that really what the torque the machine can handle?
I also have the torque and HP stats of the engine as below:
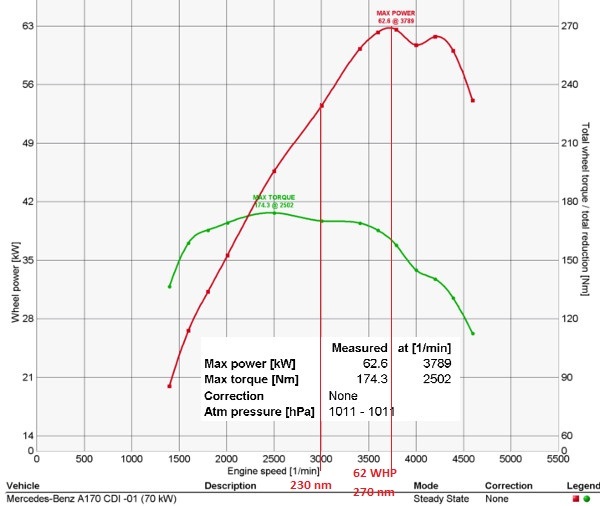
I need to find the torque of the engine related by the rated torque capacity of the wood chipper = 1384.29 Nm. @540 RPM?
Also I need to find out what engine speed can provide the max torque rating for the machine as the engine has to be reduced by a ratio through pulleys to match the max RPM of the machine. My first question is:
2) Does reducing a gear ratio, say 3.7 : 1 multiply the torque by that much? So what would happen to the machine?
If;
Torque x gear ratio = torque at the wheel
Then @ 2000 RPM the engine would provide 169.1 Nm , therefore multiply by the 3.7037 times the motor is rotating faster than 540 RPM and you have the figure 625.92 which is under the figure we have for the rated capacity of the wood chipper.
3) At the moment I am working with this:
My plan is to have a compound pulley system with 3 groove vbelt pulleys rated to at least +20% over 105 HP.
I am looking at the 2 pulley sizes of 117.5 and 305.5 and being in a drive chain to have 2 of each.
they give a ratio of 2.6 : 1 so 2 of them is 2.6 x 2.6 = 6.76.
so at 3,650 RPM it will be reduced by 6.76 times giving 539.4 rpm. So this gives peak power at peak revs.
Please can you confirm if this is right or REALLY IS ALL IN MY HEAD!!