M.sameed
Mechanical
- Aug 23, 2022
- 3
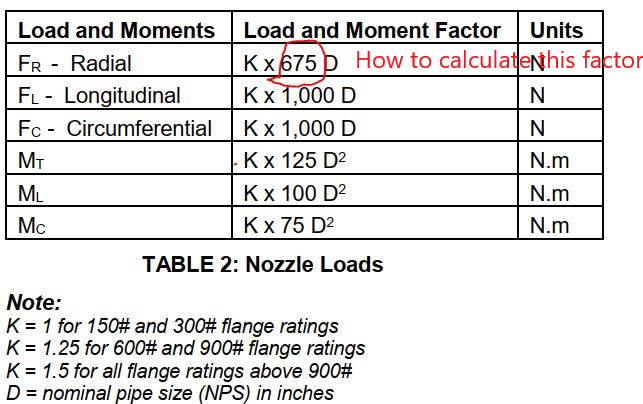
Kindly Help me understanding the nozzle load calculation
Follow along with the video below to see how to install our site as a web app on your home screen.
Note: This feature may not be available in some browsers.