Hi everyone,
I would like to perform a FEM with NX NASTRAN of this propeller on the shaft. The shaft is about 300 mm in Dia. while the propeller section is 50 x 150.
My question is about 3d mesh. If I do it with just the helix (for another type of calculation) it works very well: first I do the 2d on the starting and end section, and then the extruded 3d (with QUAD elements).
If, however, I dedicate myself to the assembly with the shaft, it happens that I am unable to create the 2D mesh of the two lateral surfaces of the propeller and I get a surface (which I interpret to be degenerate, basically a line) in the highlighted area. I have represented the line as dotted. So the 3d mesh also fails.
I don't have fillets, but I tried with fillets too.
Thanks to anyone who can give me advice!
I would like to perform a FEM with NX NASTRAN of this propeller on the shaft. The shaft is about 300 mm in Dia. while the propeller section is 50 x 150.
My question is about 3d mesh. If I do it with just the helix (for another type of calculation) it works very well: first I do the 2d on the starting and end section, and then the extruded 3d (with QUAD elements).
If, however, I dedicate myself to the assembly with the shaft, it happens that I am unable to create the 2D mesh of the two lateral surfaces of the propeller and I get a surface (which I interpret to be degenerate, basically a line) in the highlighted area. I have represented the line as dotted. So the 3d mesh also fails.
I don't have fillets, but I tried with fillets too.
Thanks to anyone who can give me advice!
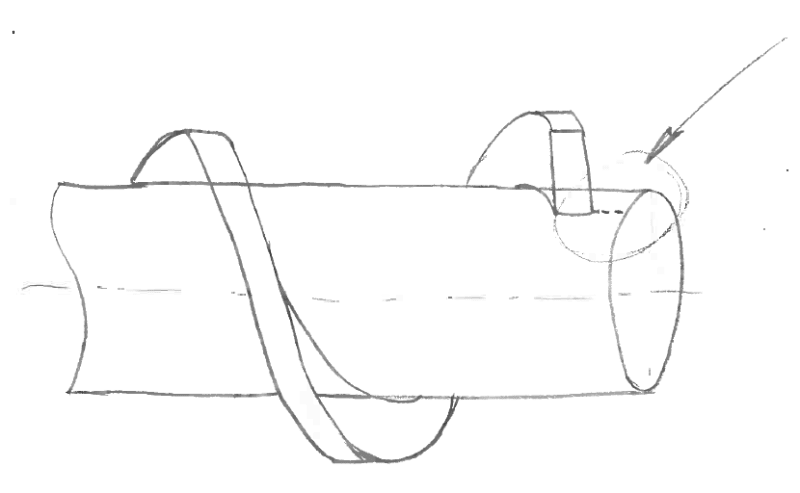