RayJohnson2
Mechanical
- Jun 22, 2015
- 32
Hi all,
I have an annoying sealing problem.
I have a test setup where a robot takes a series of plastic DUT's (Devices Under Test) one by one, and presses them against an air nozzle.
The DUT's are then subjected to an air pressure and a temperature range. The seal between the DUT and the nozzle is made by a small o-ring.
The problem is that, when the test is done and the robot removes the DUT from the air nozzle, often the o-ring sticks to the plastic DUT.
So, when the next DUT is pressed against the air nozzle, there is leakage because the o-ring is missing ...
So I should come up with a solution to keep the o-ring in its groove in the air nozzle.
Oh, and the DUT, while being pressed against the nozzle, is subjected to a temperature range of -50°C to +150°C (-58°F to +302°F).
The o-ring is quite small: inner diameter: 1.78 mm (0.07 inch), cord diameter: 1.02 mm (0.04 inch).
So a dovetail groove cross-section is pretty much impossible to tool.
I could try to glue the o-ring in the groove using silicon rubber glue (the o-ring is silicon rubber). That might work, but it will be a nuisance when the o-ring needs replacing. The remaining glue will be a mess in the groove...
For now, as a workaround, I am using a bigger o-ring, but it is actually too big for the groove so it gets damaged easily by the groove edges.
Any suggestions anyone?
I have an annoying sealing problem.
I have a test setup where a robot takes a series of plastic DUT's (Devices Under Test) one by one, and presses them against an air nozzle.
The DUT's are then subjected to an air pressure and a temperature range. The seal between the DUT and the nozzle is made by a small o-ring.
The problem is that, when the test is done and the robot removes the DUT from the air nozzle, often the o-ring sticks to the plastic DUT.
So, when the next DUT is pressed against the air nozzle, there is leakage because the o-ring is missing ...
So I should come up with a solution to keep the o-ring in its groove in the air nozzle.
Oh, and the DUT, while being pressed against the nozzle, is subjected to a temperature range of -50°C to +150°C (-58°F to +302°F).
The o-ring is quite small: inner diameter: 1.78 mm (0.07 inch), cord diameter: 1.02 mm (0.04 inch).
So a dovetail groove cross-section is pretty much impossible to tool.
I could try to glue the o-ring in the groove using silicon rubber glue (the o-ring is silicon rubber). That might work, but it will be a nuisance when the o-ring needs replacing. The remaining glue will be a mess in the groove...
For now, as a workaround, I am using a bigger o-ring, but it is actually too big for the groove so it gets damaged easily by the groove edges.
Any suggestions anyone?
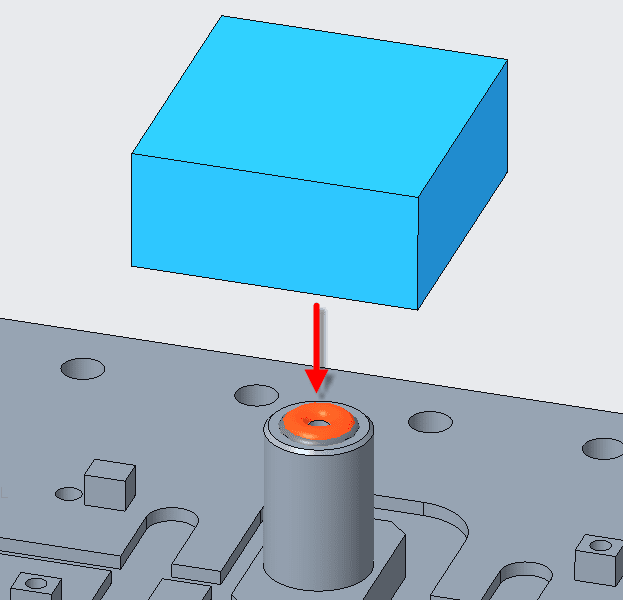
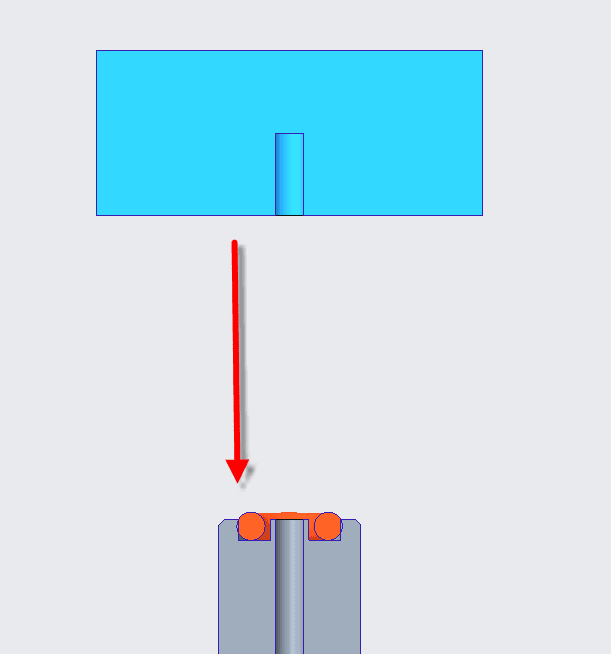
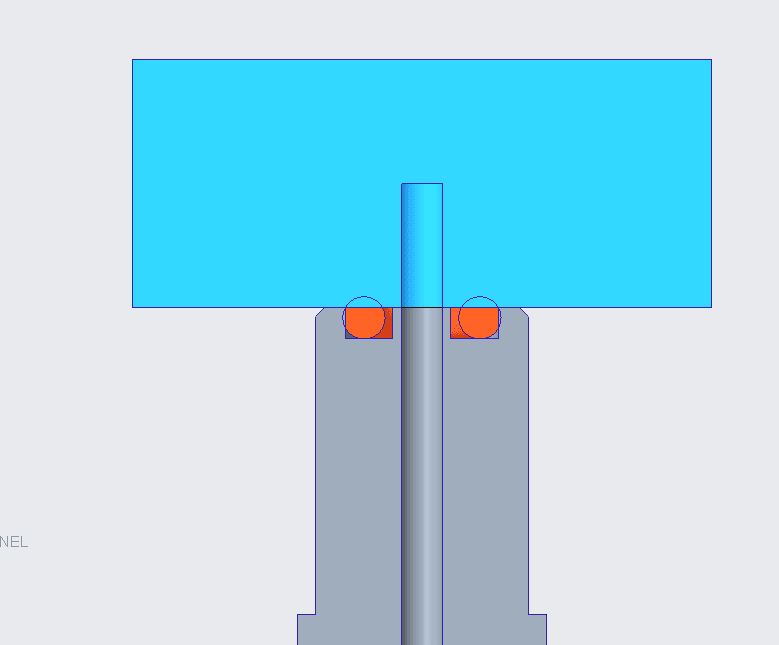
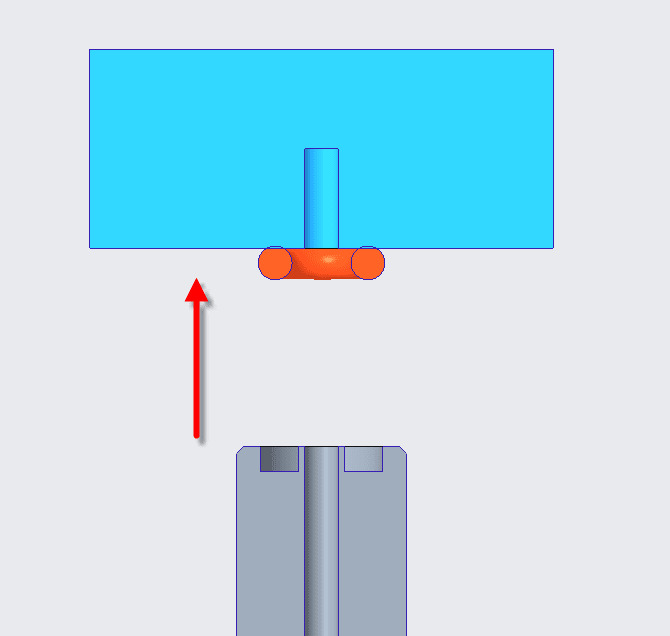