-
1
- #1
Prometheus21
Mechanical
Hello everyone,
I'm often in a position where I have to design O-ring grooves for different compressed gas applications. Radial static installation, radial dynamic installation, axial installation, dovetail grooves, half-dovetail grooves, you name it. Trelleborg and Parker handbooks are good resources in combination with industry experience.
Now, another configuration is what I guess you can call an angled seal(?) configuration. Quick example below (blacked-out part is the O-ring to indicate placement). The groove can be both a typical "square" configuration (as shown on the image below), or as half dovetail groove. The angle of orientation usually lies between 60° and 90°.
My question is this: Does any design handbooks cover this specific configuration? I know certain standards describe specific grooves for specific O-ring sizes for these configurations (e.g. ISO 5145 & CGA V-1), but not nearly as extensively as the other more common configurations. I usually deal with O-rings with a cross section between 1.78-2.4 mm, with an inside diameter <20 mm, so the stretch range is usually a bit wider than the typically recommended 2-8 %.
Don't get me wrong, I have designed these before, with no issues, by using common sense. I'm simply wondering if any handbooks cover this topic, as I've yet to find any that does.
Thank you for any input you may have.
I'm often in a position where I have to design O-ring grooves for different compressed gas applications. Radial static installation, radial dynamic installation, axial installation, dovetail grooves, half-dovetail grooves, you name it. Trelleborg and Parker handbooks are good resources in combination with industry experience.
Now, another configuration is what I guess you can call an angled seal(?) configuration. Quick example below (blacked-out part is the O-ring to indicate placement). The groove can be both a typical "square" configuration (as shown on the image below), or as half dovetail groove. The angle of orientation usually lies between 60° and 90°.
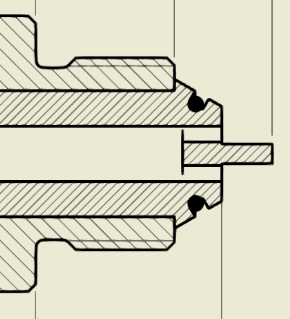
My question is this: Does any design handbooks cover this specific configuration? I know certain standards describe specific grooves for specific O-ring sizes for these configurations (e.g. ISO 5145 & CGA V-1), but not nearly as extensively as the other more common configurations. I usually deal with O-rings with a cross section between 1.78-2.4 mm, with an inside diameter <20 mm, so the stretch range is usually a bit wider than the typically recommended 2-8 %.
Don't get me wrong, I have designed these before, with no issues, by using common sense. I'm simply wondering if any handbooks cover this topic, as I've yet to find any that does.
Thank you for any input you may have.