The motor nameplate
From the nameplate, it is clear both the speeds of 1190 RPM/40 Hz & 3270 RPM/110 Hz are coming from the same base speed of 1500 RPM, 50 Hz. And yet, the motor has two different windings (Total 6 leads. One batch of 3 leads marked as T1, T2, T3 have no continuity to the other batch of 3 leads also marked as T1, T2, T3) and both windings are wound for the same base speed of 1500 RPM.
Why two windings with the same base speed? Absence of any connection diagram on the motor nameplate makes it more confusing. Are both windings supposed to be connected together to the VFD?
Also, since it is a VFD driven motor, then why only two speeds? Why not the entire range from 40 Hz to 110 Hz?
Muthu
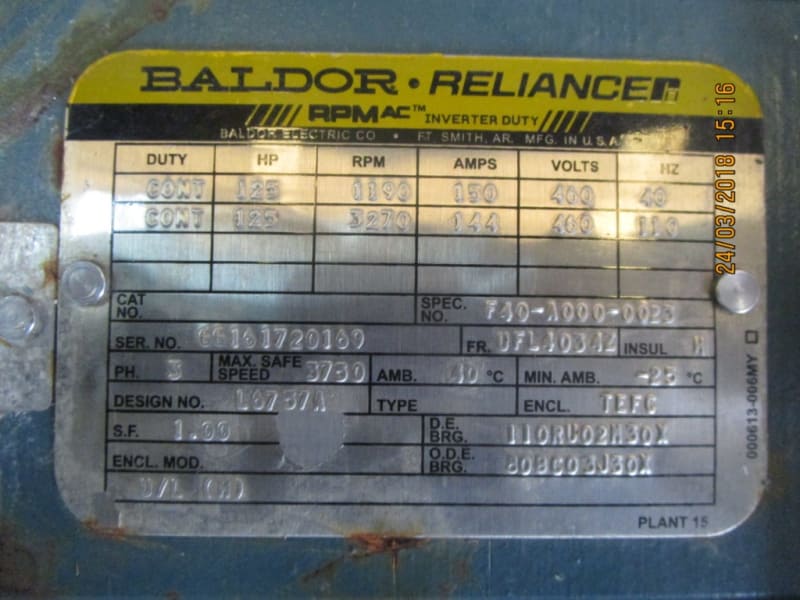
From the nameplate, it is clear both the speeds of 1190 RPM/40 Hz & 3270 RPM/110 Hz are coming from the same base speed of 1500 RPM, 50 Hz. And yet, the motor has two different windings (Total 6 leads. One batch of 3 leads marked as T1, T2, T3 have no continuity to the other batch of 3 leads also marked as T1, T2, T3) and both windings are wound for the same base speed of 1500 RPM.
Why two windings with the same base speed? Absence of any connection diagram on the motor nameplate makes it more confusing. Are both windings supposed to be connected together to the VFD?
Also, since it is a VFD driven motor, then why only two speeds? Why not the entire range from 40 Hz to 110 Hz?
Muthu