jaskamakkara
Structural
Hi guys,
I have a small indoor truss that's designed to support a short bridge that will withstand basic foot traffic. The truss is to be hidden inside a wall, and since there is no lateral restraint or returns to the wall along it's 13m span, I need the steelwork to support any lateral loads that the wall will encounter (people leaning on it, whatever). My main concern is with the out-of-plane buckling of the compression chord of the truss, since it's 13m long and there's nothing to brace it back to. I have put in some 'wind columns' which are just continuations of the vertical truss members up to the next floor of the building where they are laterally (but not vertically) supported - the idea being that these will take the lateral loads in bending, and also restrain the compression chord of the truss. Now, my question is, can I reasonably assume that these wind posts are laterally restraining the compression chord of the truss? Obviously, for the chord to buckle it would have to bend these wind posts, but I am unsure how to quantify the amount of restraint they provide. The wind posts are, at their bottoms, supported by the axial stiffness of the small floor beams that are tied back at their other ends either to a stiff beam HEB220 - so very stiff in it's minor axis - or fixed into another wall.
Hopefully this is clear, the picture below should help:
Any help would be appreciated!
I have a small indoor truss that's designed to support a short bridge that will withstand basic foot traffic. The truss is to be hidden inside a wall, and since there is no lateral restraint or returns to the wall along it's 13m span, I need the steelwork to support any lateral loads that the wall will encounter (people leaning on it, whatever). My main concern is with the out-of-plane buckling of the compression chord of the truss, since it's 13m long and there's nothing to brace it back to. I have put in some 'wind columns' which are just continuations of the vertical truss members up to the next floor of the building where they are laterally (but not vertically) supported - the idea being that these will take the lateral loads in bending, and also restrain the compression chord of the truss. Now, my question is, can I reasonably assume that these wind posts are laterally restraining the compression chord of the truss? Obviously, for the chord to buckle it would have to bend these wind posts, but I am unsure how to quantify the amount of restraint they provide. The wind posts are, at their bottoms, supported by the axial stiffness of the small floor beams that are tied back at their other ends either to a stiff beam HEB220 - so very stiff in it's minor axis - or fixed into another wall.
Hopefully this is clear, the picture below should help:
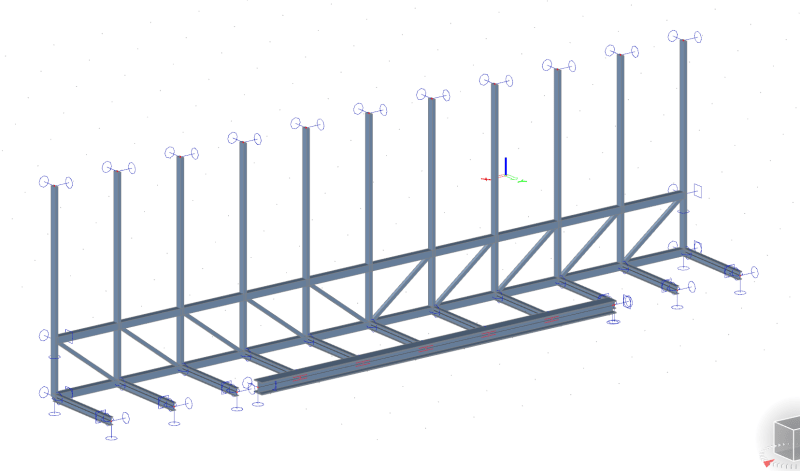
Any help would be appreciated!