Good Evening Engineers,
I am designing a commercial carport with supports only at the back. Below is a picture of roughly what I am trying to achieve. The location has a relatively low snow load of 1.2kPa but it poses a challenge! I have tried modelling a couple of options and I am wondering what you guys think. What is interesting is my designs are based on a post at every stall (10') while the picture below shows one at every 3 stalls! Maybe that area has no snow. Loads shown are SLS.
Question1: What is an acceptable deflection for something like this? Since no finishes on the underside, I wonder if L/240 would be acceptable.
Question2: This is a 2D design, I wonder if once the diaphragm goes in or if I X-brace them together, they will perform better?
The first option is great but leads to a large uplift on the back column which I'll have to check if I can resist by pouring one footing for both piers
The second option I think looks cooler but I have found so far that the moment connection at base would be quite large. I placed the post 4' in from the back to decrease the moment but the moment is still so large that it would require sizeable footing that would not fit in between cars. Modelling the carport as shown in the picture yields a ridiculous moment at base.
I am designing a commercial carport with supports only at the back. Below is a picture of roughly what I am trying to achieve. The location has a relatively low snow load of 1.2kPa but it poses a challenge! I have tried modelling a couple of options and I am wondering what you guys think. What is interesting is my designs are based on a post at every stall (10') while the picture below shows one at every 3 stalls! Maybe that area has no snow. Loads shown are SLS.
Question1: What is an acceptable deflection for something like this? Since no finishes on the underside, I wonder if L/240 would be acceptable.
Question2: This is a 2D design, I wonder if once the diaphragm goes in or if I X-brace them together, they will perform better?
The first option is great but leads to a large uplift on the back column which I'll have to check if I can resist by pouring one footing for both piers
The second option I think looks cooler but I have found so far that the moment connection at base would be quite large. I placed the post 4' in from the back to decrease the moment but the moment is still so large that it would require sizeable footing that would not fit in between cars. Modelling the carport as shown in the picture yields a ridiculous moment at base.
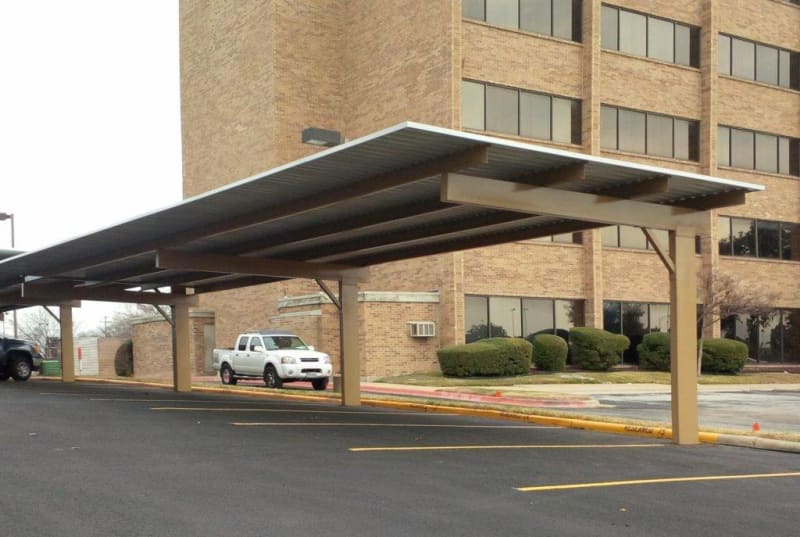

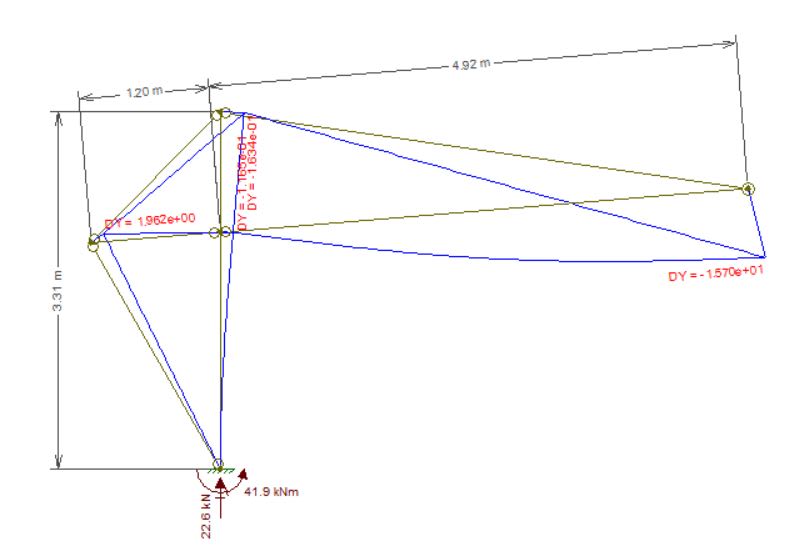