-
1
- #1
Vikram 1971
Industrial
Currently using 335 KW 3 Phase Inductor motor (415V 563A 740 RPM) without any VFD in Hot Rolling Mill.
Thinking about investing in VFD to drive the above motor to enjoy saving due to VFD.
The motor operates in 20%-50% load for 50% percent of time. The current peaks up to 800-900 A for 1 seconds or less in every 10 seconds. Motor starting current is controlled via resistance shorting of slip Rings. (Motor runs idle-No load for atleast 20min in an hour)
My Question is -
1.) Whether VFD will be able to help in energy saving??
2.) I have decided a VFD (ABB Manufactured) rated for 600A. Will it be able to momentarily (less than 1 second) supply 800-900A during over loads???? What will happen in overload? will it Stop or Slow the process???
Attached the current reading during Normal operation.
Thanks in advance!!!!!!!!!
This is a big investment, I just want to be sure whether it worth it or just a marketing gimmick.
Thinking about investing in VFD to drive the above motor to enjoy saving due to VFD.
The motor operates in 20%-50% load for 50% percent of time. The current peaks up to 800-900 A for 1 seconds or less in every 10 seconds. Motor starting current is controlled via resistance shorting of slip Rings. (Motor runs idle-No load for atleast 20min in an hour)
My Question is -
1.) Whether VFD will be able to help in energy saving??
2.) I have decided a VFD (ABB Manufactured) rated for 600A. Will it be able to momentarily (less than 1 second) supply 800-900A during over loads???? What will happen in overload? will it Stop or Slow the process???
Attached the current reading during Normal operation.
Thanks in advance!!!!!!!!!
This is a big investment, I just want to be sure whether it worth it or just a marketing gimmick.
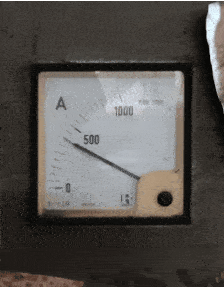