Hi All,
I am currently working to provide an overplating for an I-section that is a historic section of 4"x3" RSJ.
As you know, the historic sections have curvature between the web and the flanges (around 95 degrees). See the screenshot below for details.
The beam that I am dealing with has isolated holes to its web, hence I am proposing to overplate with angle section to cover these holes and to provide additional strength as requested by the client.
My question is that, since the top flange is coming at an angle and it is not straight, how is it practical to propose this repair detail? Is it the case that providing a packer plate to make this happen the right approach? Or even if the beam is slightly angled at the flanges, the contractor would be able to fix the angle plate to the top flange without issues?
I have provided screenshots below for information. It would be great if someone can help on this.
I am currently working to provide an overplating for an I-section that is a historic section of 4"x3" RSJ.
As you know, the historic sections have curvature between the web and the flanges (around 95 degrees). See the screenshot below for details.
The beam that I am dealing with has isolated holes to its web, hence I am proposing to overplate with angle section to cover these holes and to provide additional strength as requested by the client.
My question is that, since the top flange is coming at an angle and it is not straight, how is it practical to propose this repair detail? Is it the case that providing a packer plate to make this happen the right approach? Or even if the beam is slightly angled at the flanges, the contractor would be able to fix the angle plate to the top flange without issues?
I have provided screenshots below for information. It would be great if someone can help on this.
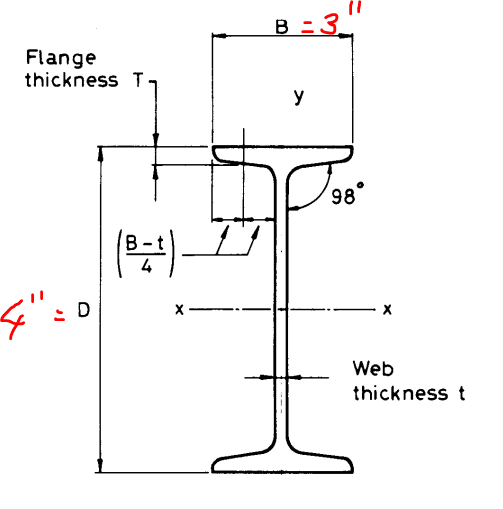
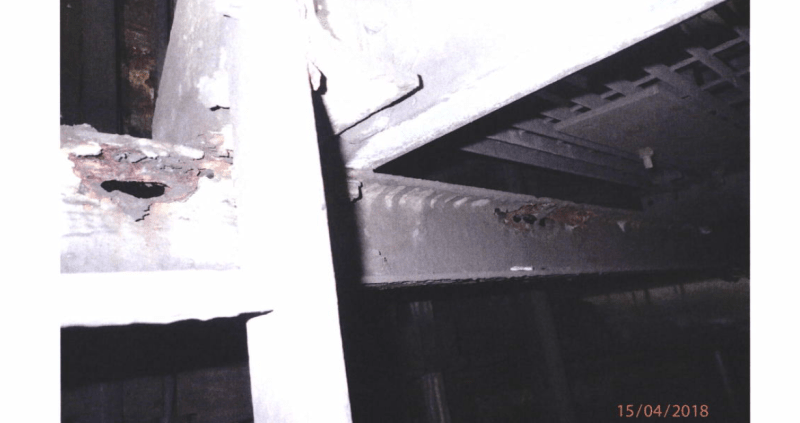
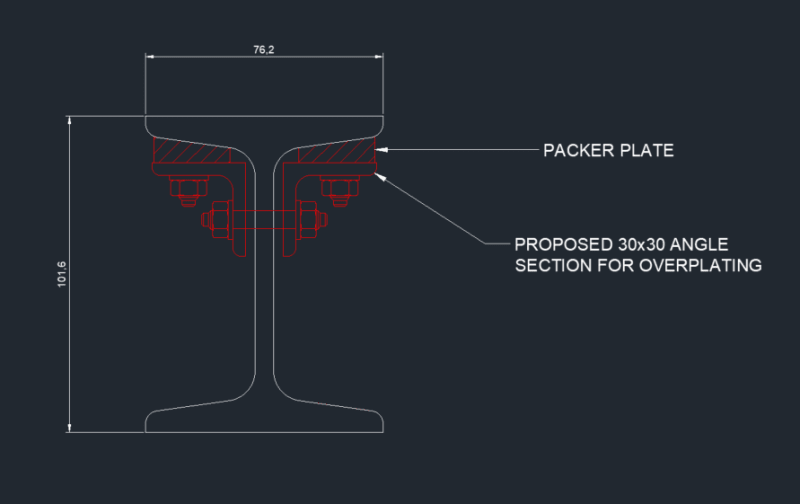