threeReefs
Electrical
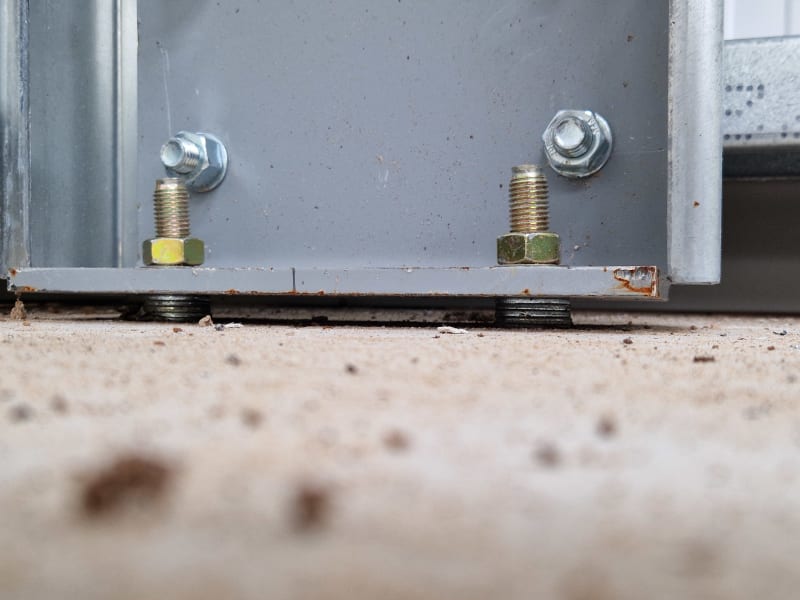
I'm having a forestry building put up, and the contractors have done this to compensate for slight variations in slab height. The building is steel-frame, 14m x 13m, 4m high. You're looking at the foot of a cold-rolled steel pillar - one of 10 structural pillars forming the main frame of the building - bolted to an L-plate which is in turn bolted to the slab.
I am an electrical rather than a structural engineer, but this looks wrong to me : the columns do not touch the slab, so the L-plate isn't just locating them, it's carrying the load, and that load will now go only through the washers - point load, and no stability in the forward/backward direction and not a whole lot in the other. OK, the building is rigid so it's not trying to hinge forward or backward, but I still don't like the look. Can someone tell me whether I should worry or is this fairly normal practice ?
Thoughts much appreciated.
Richard