jrhodges
Aerospace
- Sep 2, 2015
- 4
I am looking for some help with the following situation (see image). I've been looking through ASME Y14.5-2009 and other guides and can't find precisely what I'm looking for.
I'm trying to determine how the note, "Perfect form not required at MMC" effects this tolerance scheme. I'm primarily concerned with how this affects envelope and if this may have an effect on the thickness variation within the part itself. Ultimately I'm trying to see what could this part actually look like?
Thanks for your help!
I'm trying to determine how the note, "Perfect form not required at MMC" effects this tolerance scheme. I'm primarily concerned with how this affects envelope and if this may have an effect on the thickness variation within the part itself. Ultimately I'm trying to see what could this part actually look like?
Thanks for your help!
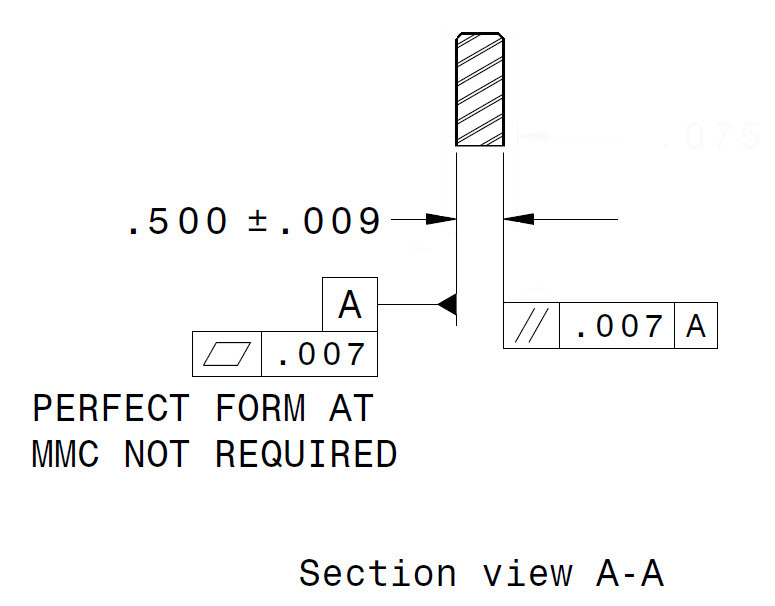